

Maximizing manufacturing efficiency - unlocking the power of Overall Equipment E...
source link: https://diginomica.com/maximizing-manufacturing-efficiency-unlocking-power-overall-equipment-effectiveness-oee
Go to the source link to view the article. You can view the picture content, updated content and better typesetting reading experience. If the link is broken, please click the button below to view the snapshot at that time.
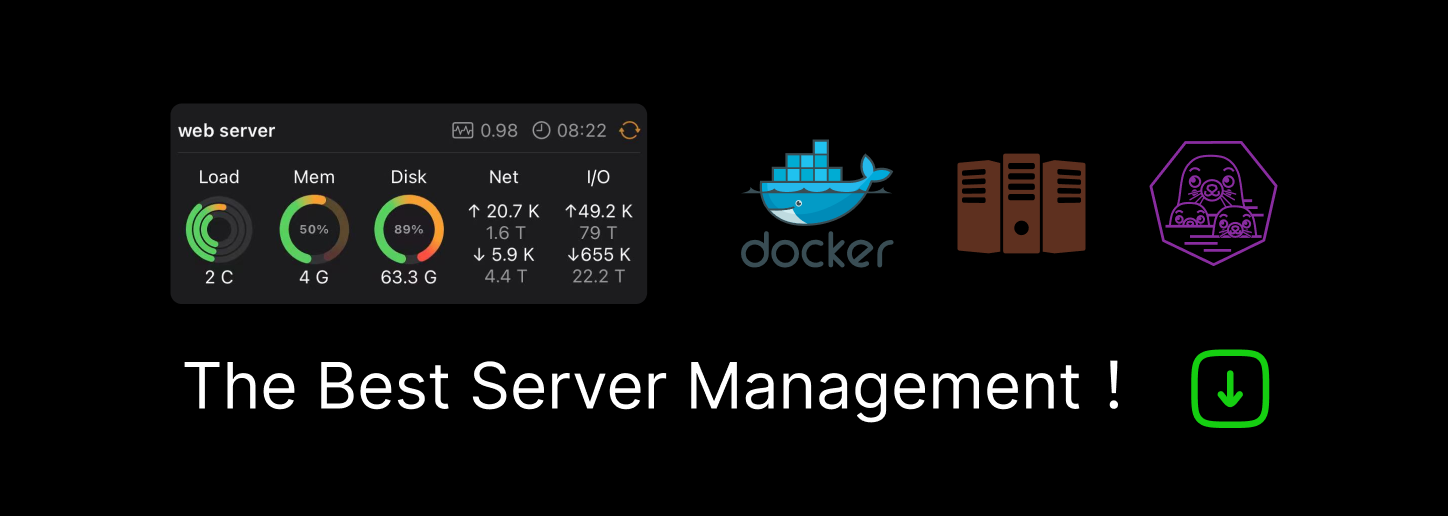
Maximizing manufacturing efficiency - unlocking the power of Overall Equipment Effectiveness (OEE)

(© Gorodenkoff - Shutterstock)
Manufacturers are constantly seeking ways to optimize their operations and enhance productivity as a means of fighting in increasingly competitive environments. One key metric at the heart of this effort is Overall Equipment Effectiveness (OEE) – but too many manufacturers have not made optimal use of OEE.
OEE provides valuable insights into the performance of not only single pieces of manufacturing equipment, but also production lines and entire facilities, enabling organizations to identify and address inefficiencies, reduce downtime, and maximize productivity.
While OEE is not new, it has traditionally been the preserve of large manufacturers with large budgets. Most typically, through largely manual processes, a lot of manufacturing floors are running at around 60% OEE. But we’re living in a digital age, so which technologies can be used to fill in the gaps and help smaller organizations to move towards the Holy Grail of 90% OEE? Even the best pieces of equipment need regular maintenance which realistically means an objective of 90% is a good target – so let’s take a look at how we can move a little closer to that goal.
Understanding the Components of OEE
OEE is a comprehensive metric that measures the effectiveness of equipment in three critical dimensions: availability, performance, and quality. By combing these three pillars that give an impression of an organization’s potential for high quality output, it’s possible to gauge where the company is, in terms of resilience and ability to capitalize on market opportunities.
However, it’s one thing to be able to look back and reflect on whether last week, or last month, went well. It’s another thing altogether to be able to filter this information into day-to-day, hour-to-hour operations in order to maximize production as it’s happening, not in the future after losses have potentially occurred. Most frequently the issues affecting OEE will be ‘short stops’ and quality defects and the sooner they can be picked up and rectified, the better the outcomes will be. Larger scale machine failures may occur less frequently, but if these are the factors most affecting OEE, a fuller scale maintenance programme will be needed.
In order to take immediate action, data needs to become the lifeblood of these operations. But a move to digital isn’t necessarily simple. When looking at places to start on this mission, the ‘six big losses’ associated with production are as good a place as any.
The six big losses are a valuable framework for manufacturers to identify and address inefficiencies within their production processes. These losses include equipment failure, setup and adjustment time, idling and minor stoppages, reduced speed, process defects, and reduced yield. Understanding that this is where losses occur is one thing, but being able to mitigate them before too much damage is done it quite another.
Therefore finding ways of recognizing when these losses are happening (or even about to happen) will have a significant impact. This is where data capture and systems integration starts to connect the dots on the shop floor. For example, if equipment ‘failure’ is re-defined as a marginal reduction in output or quality, not when things stop working, the outcomes are huge. Sensor data that can indicate even the slightest changes can be the trigger for this conclusion. Capturing the data and integrating it into a central system that can process the relevance of the information enables these realizations to happen.
Setting Effective Key Performance Indicators (KPIs) and Monitoring
To effectively manage OEE, all KPIs need to be robustly evaluated to ensure that they indicate progress towards higher OEE numbers. Once that is assured, the monitoring systems to handle those KPIs can be designed. Defining KPIs that align with business objectives and accurately reflect the desired outcomes is clearly crucial – at times, though, KPIs and means of measurement have been where disconnects can happen. Establishing a policy that associates reasons with downtime longer than a specified duration, such as two minutes, enables organizations to differentiate between availability and performance losses accurately.
How Technology Can Help Drive OEE Success
Technology can help to move organizations closer to the full potential of OEE. Data collection and analysis lie at the heart of this mission, which makes integrating sensors and IoT devices with manufacturing equipment a priority. This allows the real-time data acquisition that facilitates timely decision-making and proactive maintenance.
By continuously monitoring – and, crucially, seeing – equipment performance, organizations can identify patterns, detect anomalies, and implement preventive measures to minimize downtime and optimize productivity. Advanced analytics capabilities further enable predictive maintenance, reducing the risk of unexpected breakdowns and maximizing the utilization of manufacturing assets.
Moreover, connecting multiple production stages and systems fosters a holistic view of the manufacturing process. Many modern pieces of automation and equipment have the option or come with a control tower created by the vendor. A single piece of equipment can operate “in the green” but OEE scores can still be low, especially when defects are the major issue. Integrating equipment and zones allows for seamless data exchange, enabling organizations to identify bottlenecks, streamline workflows, and optimize resource allocation across the entire line or facility.
Realizing the Benefits
Implementing OEE effectively provides a multitude of benefits. By identifying and addressing the six big losses, organizations can optimize equipment utilization, reduce downtime, and improve overall productivity. Enhanced quality control minimizes process defects and ensures that products consistently meet customer expectations. Additionally, by leveraging technology to monitor and analyze performance, organizations can achieve proactive maintenance, reducing costs associated with reactive repairs and minimizing the impact of unplanned downtime.
The good news is that it’s possible to start small, see benefits and build on them. But as the manufacturing industry continues to change rapidly, reacting to shifts in demand, government incentives and price fluctuations, maximizing efficiency is paramount to maintaining a competitive edge. Overall Equipment Effectiveness (OEE) offers a chance to comprehensively evaluate and enhance equipment performance and push towards those bigger business goals.
Recommend
-
3
July 16, 2021 ...
-
3
Andrei F. on Twitter: "I do think Intel has an overall efficiency advantage in every-day use-cases due to AMD's super crappy idle and 1C package power overhead. The narrative out there seems to be wrong."Don’t miss what’s happening
-
4
Calidus and IFS – a partnership that is changing defense equipment design, manufacturing and delivery ...
-
0
Sustainable EnergyEV car manufacturing jumps in the UK but overall production sinks to 65-year lowPublished Thu, Jan 27 20229:22 AM EST
-
8
67W vs 96W Power Adapter Dimensions? Which is overall better?
-
5
Shashank Mandlik May 25, 2023 3 minute read...
-
3
Azman Nabi June 9, 2023 3 minute read
-
8
A Deep Dive into Bit’s Version Control: Maximizing Efficiency for Large TeamsHow is Bit’s Version Controlling System is improving development efficiency in teams?
-
7
Meetings are a crucial aspect of software engineering, serving as a collaboration, communication, and decision-making platform. However, they...
-
6
Misc Maximizing Efficiency: Automating Your...
About Joyk
Aggregate valuable and interesting links.
Joyk means Joy of geeK