

Modernization is vital to prevent supply chain businesses from being left behind...
source link: https://diginomica.com/modernization-vital-prevent-supply-chain-businesses-being-left-behind-slow-lane
Go to the source link to view the article. You can view the picture content, updated content and better typesetting reading experience. If the link is broken, please click the button below to view the snapshot at that time.
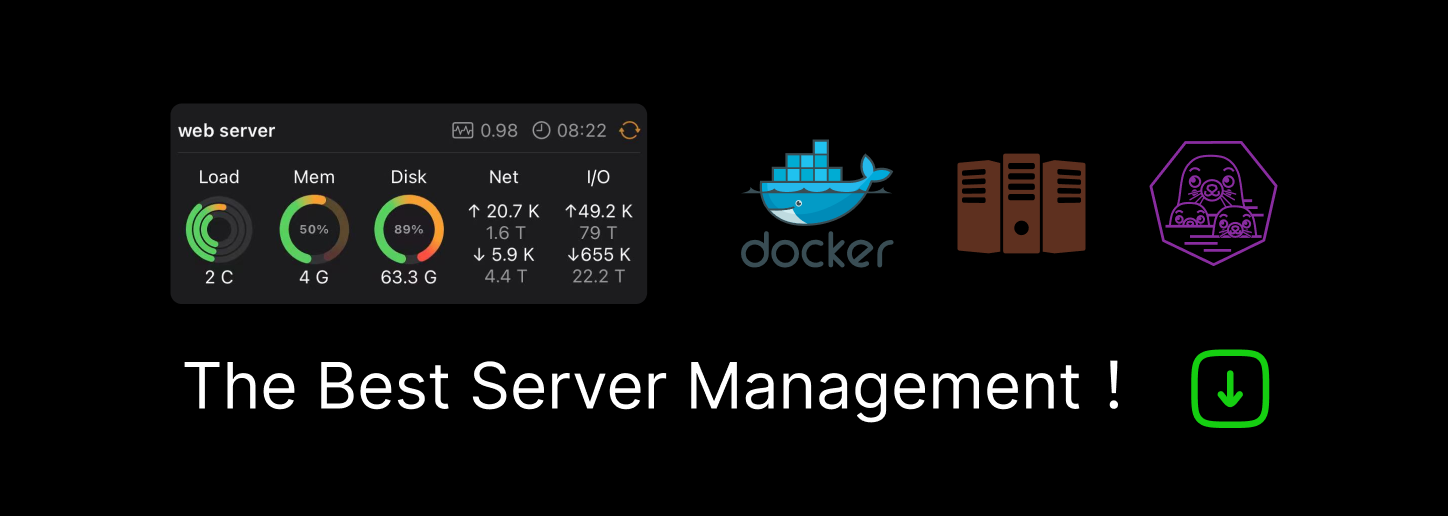
Modernization is vital to prevent supply chain businesses from being left behind in the slow lane

(© zhu difeng - Shutterstock)
Time is money. And in the world of logistics, speed is everything. Whether it’s ensuring something reaches its final destination or forms a vital link in an increasingly complex supply chain, the pressure remains the same.
Promising to get things safely from A to B in the shortest time is integral to competitive advantage.
But vehicles can only go so fast. And for those firms simply searching for ever-faster delivery times, the emphasis needs to be on efficiency rather than cutting corners in a bid to meet deadlines. Otherwise, the rush to meet ever-tighter schedules could lead to errors, foul-ups — or worse.
For many operators, the trick is not just to speed up delivery, but to increase the speed at which a business operates. That way, it becomes more efficient, responsive, and better able to weather the ups and downs of complex supply chains.
Modernizing manual processes
One of the biggest brakes to digital transformation within vehicle fleets in the logistics industry is their continued reliance on manual processes.
Even today, drivers are expected to complete everyday tasks such as vehicle walkarounds — where they visually check vans and lorries for defects — using a clipboard and pen to jot down any issues. In many cases, deliveries are still signed for, with a piece of paper handed to the customer and one physically taken to head office for processing and filing.
What makes this approach even more anachronistic, is that most drivers have a smartphone in their back pocket to make financial transactions, shop online, and stream digital services. All of these tasks — conducted when they’re safely parked up, of course — are done safely, securely, and in real-time.
And yet for their work, drivers are still expected to rely on paper processes when there’s little doubt that digitizing these using easy-to-use apps can save huge amounts of time.
For example, US-based American Cementing — which operates more than 400 vehicles and 1,000 trailers — made its entire business paperless bydigitizing all its documentation.
By digitizing everything — from fuel receipts and vehicle maintenance alerts to payroll and driver coaching — American Cementing managed to bin 13,000 pieces of paper and saved $60,000 a year. In fact, it also saved over 1,600 hours a year in administrative time alone by going paperless.
They’re not alone. US-based timber and building supplies company UFP Industries saved a small fortune by adopting paperless driver workflows and proof of delivery (POD). As Larry Ogg, Director of Logisics at UFP noted:
We think that, conservatively, this is probably a $600,000 saving for us in administrative workload. Having that real-time visibility has really helped us take track and trace to the next level.
In the UK, Lanes Group — the leading wastewater utility solutions provider, which employs over 4,000 people and boasts a turnover of more than £430 million — rolled out smart solutions across the business that have led directly to a more efficient, safer, and cost-effective business.
Thanks to a focus on digital transformation, it’s automated many of the manual processes across its operation. As a result, drivers spend less time on administration and filling out paper forms or submitting documents in person. Instead, they spend more time focusing on improving their driving and completing tasks safely.
And alongside savings in insurance costs and other productivity gains, the firm has made savings of more than £300,000 thanks to real-time data insights. As Wayne Earnshaw, Chief Executive Officer, Lanes Group said:
From keeping asset downtime to a minimum to automating manual tasks and resolving incidents in hours versus weeks, we’re spending less time chasing information and more time using it to make more informed business decisions.
The versatility of an enterprise-scale connected platform
All this can be done because firms are no longer looking to buy off-the-shelf solutions that address single problems, such as one system for payroll, another for HR, and a telematics program to monitor fuel costs.
Instead, they’re opting for a single platform that unifies their entire fleet operation, feeding information into a central hub where it can be accessed where it’s needed most.
A prime example is logistics company Weinhut GmbH, which has been operating from Neutraubling, Germany, for over 15 years. Today, the company has a fleet of almost 100 vehicles that between them clock up some 2.5 million miles a year. As a contractual partner of UPS, Weinhut delivers daily around 12,800 packages in Regensburg and the surrounding region, as well as courier and direct deliveries.
Weinhut used to rely on a tracking system that only sent a GPS signal when the vehicle moved.
Today, they’re using a GPS fleet tracking system and front-facing dash cams that allow the entire fleet to be managed on a single platform.
This system enables fleet managers to track all vehicles, automatically log on-board diagnostics (OBD) data at any time, check the amount of fuel in the tank, assess dash cam footage if accidents occur, monitor drivers' route times, and schedule a visit to the workshop for servicing to maximize the time they are on the road.
It couldn’t be further from the pen and paper process still used by so many firms in the industry.
No sooner has a driver captured delivery photos, made any notes, and captured electronic signatures using a smartphone or tablet, all that data is instantly uploaded to a central dashboard.
It doesn’t matter what is being delivered — be it small consumer items or giant loads of raw materials. Knowing exactly where vehicles and their loads are in the supply chain and being able to reassure customers that shipments will hit delivery windows is a key driver to improving efficiency.
Instant availability makes for safer driving
The same is true of video footage from dash cams. If an incident does occur, the images are uploaded immediately to the cloud. These can be viewed within seconds by managers, and in many cases help to exonerate their drivers within minutes.
This means managers don't have to waste precious time retrieving dash cams for vehicles so they can then download footage from internal storage. Drivers can also send an immediate alert to managers via a panic button to speed up response times and log the immediate aftermath of any incident to provide a contemporaneous report backed up with pictures.
Without this technology, drivers would be forced to handwrite accident reports along with diagrams and sketches to explain what happened.
Connected telematics, on the other hand, provides video of the incident, the events leading up to it, the view of the driver, plus vehicle data, speed, and road conditions in 15 minutes. It is the availability of this detailed information in the 'golden hour' after an incident that can prove to be so vital in exonerating drivers in not-at-fault or fraudulent accidents.
By replacing bits of paper with easy-to-use driver apps, technology can modernize a business and speed up essential back-office functions. Anything logged by a driver is immediately sent to a central dashboard where it can be viewed and acted upon across the whole business.
In a world where time is money, digitizing back-office functions and speeding up business processes is now part and parcel of moving goods from A to B.
Recommend
About Joyk
Aggregate valuable and interesting links.
Joyk means Joy of geeK