

The Intelligent Enterprise in Mining Industry – Mining Savings on Operational As...
source link: https://blogs.sap.com/2023/01/11/the-intelligent-enterprise-in-mining-industry-mining-savings-on-operational-assets-part-1-2/
Go to the source link to view the article. You can view the picture content, updated content and better typesetting reading experience. If the link is broken, please click the button below to view the snapshot at that time.
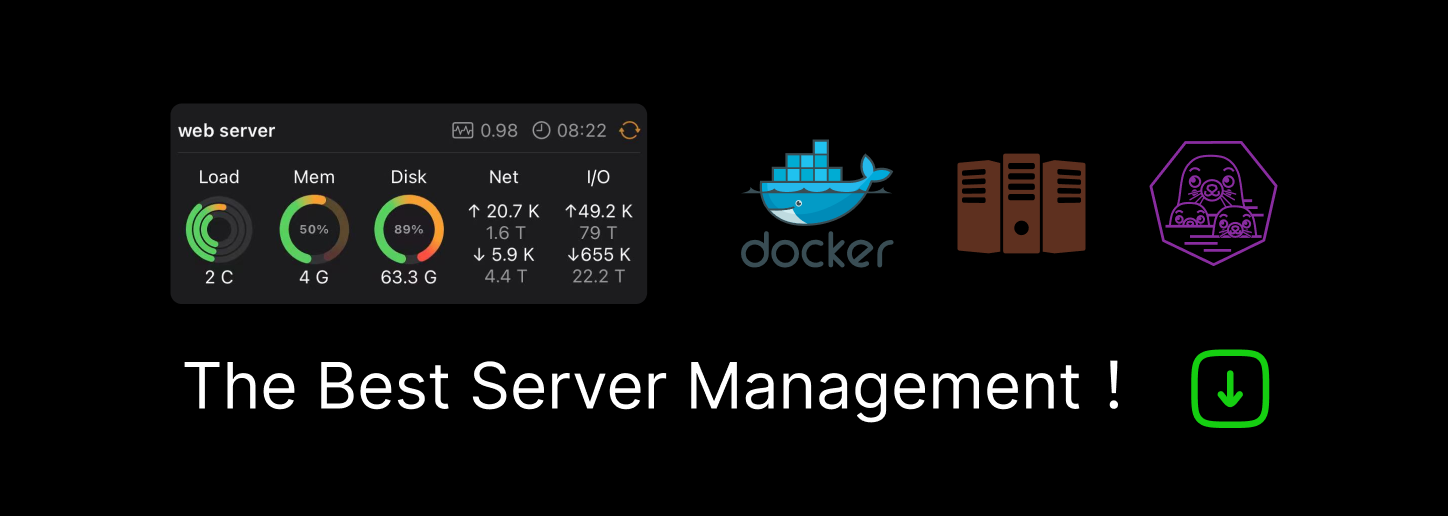
The Intelligent Enterprise in Mining Industry – Mining Savings on Operational Assets (Part 1/2)
As a business process consultant for SAP Enterprise Asset Management/Intelligent Asset Management, I am close in touch with many customers running various solutions to manage their assets. Common goals are to achieve high availability of their industrial equipment and ensure safe and resilient operations while managing the costs.
For the mining industry, the pace of change is picking up rapidly. Market volatility can deliver record profits in one particular year, turn sideways the following year, and keep changing in between. Today, the industry faces supply chain disruptions, workforce shortages, increasing sustainability regulations, and reporting requirements.
How can mining companies become agile to enhance asset performance while simplifying operations? In this blog, I will introduce onboarding from best practices to the following best practices. With the right platform, a mining enterprise can dramatically improve the availability of its manufacturing assets – a critical factor in long-term success, particularly for heavy industry.
Challenge#1: Decision-making based on experience and intuition
Making decisions during mining usually requires years of industry experience, which is even more challenging with disparate systems. Managing capital assets generally refers to availability, risk estimation, and health. Thanks to the existing ERP solutions, mining companies can integrate different methods (such as IoT) to enable analytics and end-to-end processes:
- Mixed and match – automated and manual data integration.
- Data and process based on system domain.
- Utilizing batch job.
- Pulled data into one spreadsheet.
However, to take analytics to the next level, the next best practice is to leverage a predictive approach to gain real-time visibility into operations:
- Combine planning and sales for informed decisions based on profit.
- Improve planning cycles from days to hours.
- Analyze data through embedded analytics in real-time rather than monthly spreadsheets.
- More predictive insight.
Industry 4.0 reshapes the ability of asset management. For example, mining companies can optimize maintenance planning strategies using AI-based predictive maintenance software such as SAP Asset Performance Management. Onsite managers could proactively plan the utilization of assets and act on equipment failures based on risk and reliability management. It provides the ability to anticipate changes by evaluating data from complex machinery, which could potentially reduce or prevent asset downtime.
Challenge#2: Limited collaboration from planning to executing
There is no doubt that collaboration drives innovation. There is an increasing need to eliminate paper-based processes to digitalize asset maintenance activities and enhance mining collaboration with the frontline mining workforce. Global operations centers can now bridge the geographical gap with the distributed workforce to oversee the operations and provide maintenance instructions. Another factor to consider is to utilize mobile offline capability, which enables miners to quickly access work orders and asset data. With the advancement in connectivity, intermittent connection and offline data sync are overcome, especially in underground mining. Whenever the connection is back up, the system will trigger synchronization automatically.
Regarding collaboration with suppliers, the best practice is to use business networks and cross-company collaboration through multiple solutions. Mining production and maintenance can be more preventive by sharing information through file exchanges. After achieving this, the next practice is to adopt digital twins and extend collaboration to equipment manufacturers and other service providers. A single collaboration platform can have a 360 view of equipment and exchange asset performance feedback simultaneously. It connected enterprises to act quickly on any sudden changes.
In part 2, I will discuss how to focus on customer needs and build a sustainable business in the mining industry.
- Bringing Next Practices Today: Every enterprise needs to develop new business models to avoid disruption, gain efficiencies to fund innovation, and transform mission-critical systems with lower business risk.
- Optimize with Best Practices: A stable and reliable business foundation to run end-to-end processes as effectively and efficiently as possible.
- Transform with Next Practices: An agile and flexible platform for innovating quickly in the areas where differentiation drives competitive advantage.
Looking forward to having more asset management discussions!
@Sandy (Sandy Huang Former Member
Recommend
About Joyk
Aggregate valuable and interesting links.
Joyk means Joy of geeK