

Get a common view of asset maintenance across your chemicals business
source link: https://www.infor.com/blog/get-a-common-view-of-asset-maintenance-across-your-chemicals-business
Go to the source link to view the article. You can view the picture content, updated content and better typesetting reading experience. If the link is broken, please click the button below to view the snapshot at that time.
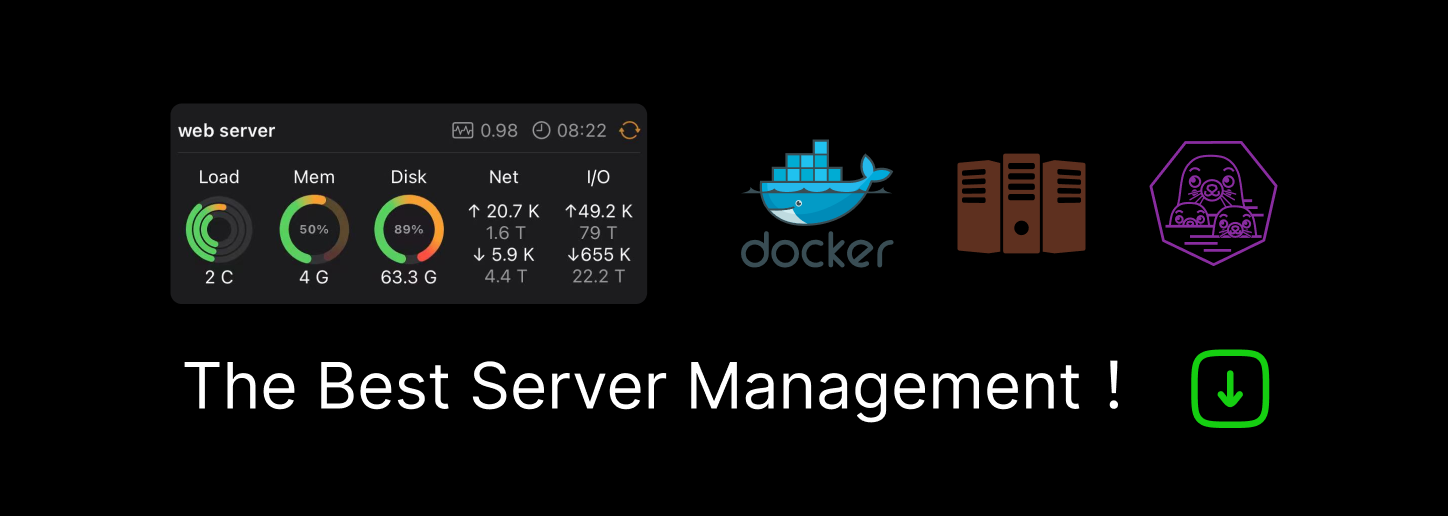
Get a common view of asset maintenance across your chemicals business
In this blog series we’ll dig deeper into the different perspectives and priorities of asset maintenance between the C-suite and various functional groups in the chemicals industry. We’ll also review the operational and financial benefits of deploying a modern EAM solution.
Asset-intensive industries operate extremely complex plants using assets that are often old and require precise care. Along with this, the average lifespan of assets continues to increase, allowing companies in industries such as chemicals, oil and gas, materials, and pulp and paper, to avoid or delay heavy capital expenditures. But older assets also means higher cost for maintenance and the workforce to maintain the assets and equipment.
The wide variety of equipment and interconnected assets used to run asset intensive plants come with their own unique failure modes and complex sets of maintenance, safety, and compliance requirements that need to be maintained—while ensuring maximum uptime for the plants and operations. Unfortunately, these requirements carry varying meanings and have different priorities between the C-suite and various functional groups, such as operations management, maintenance staff, planners, and everyday operators.
At the corporate level, CEOs, COOs, and CFOs often think in terms of return on assets (ROA), return on net assets (RONA), return on capital expended (ROCE), return on invested capital (ROIC), and more. CIOs in particular, like using a single platform for their enterprise resource planning (ERP) and enterprise asset management (EAM) systems.
Operations management teams on plant floors, on the other hand, are primarily concerned with overall equipment effectiveness (OEE), total effective equipment performance (TEEP), availability and uptime, and total maintenance cost as a percent of replacement asset value (RAV).
Meanwhile, maintenance teams focus on maintenance costs, maintenance personnel hours and costs, and overtime costs. Other, more sophisticated maintenance teams operate in terms of corrective maintenance costs and hours vs. preventive maintenance costs and hours, and condition-based maintenance costs and hours. These teams also focus on systematic work order management; they look at planned work vs. unplanned work, reactive work vs. proactive work, work order aging, and work order cycle times. Leading chemicals companies also collect and decipher data for preventive maintenance and predictive maintenance, overdue work orders, and preventive maintenance and predictive maintenance yield.
While different teams focus on different measures, one set of criteria that all functions operating at a plant (and upper management) can agree on is safety, compliance, and reliability. But many companies struggle to define the right KPIs to measure this. Or even worse, the don’t have access to the right data, or are unable to collect it to track performance accurately.
So how does a chemicals company handle so many different perspectives and functions at the same time, invest money in the right places, see quick results for each stakeholder, and measure ROI? Download our best practice guide “Maximize asset utilization—Get a common view of asset maintenance across your chemicals business” to learn more.
Recommend
About Joyk
Aggregate valuable and interesting links.
Joyk means Joy of geeK