

Increasing Supply Chain Resilience: Real-World Insights and Methods to Stay on T...
source link: https://blogs.sap.com/2023/06/23/increasing-supply-chain-resilience-real-world-insights-and-methods-to-stay-on-track/
Go to the source link to view the article. You can view the picture content, updated content and better typesetting reading experience. If the link is broken, please click the button below to view the snapshot at that time.
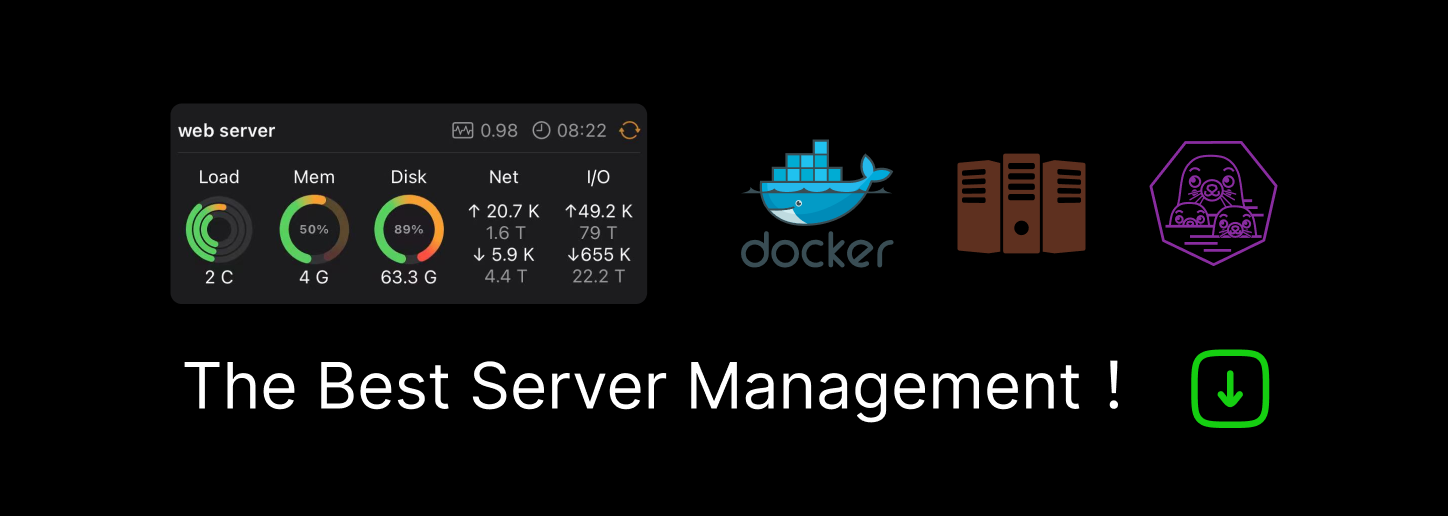
Increasing Supply Chain Resilience: Real-World Insights and Methods to Stay on Track

Motivation
As the well-known expression “Never change a winning team!” suggests, no one likes to adjust a system once it is running smoothly. However, sometimes there are forces beyond a company’s control that make it necessary to rethink processes and supply chain setups. These forces can occur suddenly (for example, a fire in a production site, a blockade in an important transport hub, or a shipper going bankrupt) or may build up slowly (for example, long-lasting heatwaves, conflicts with a key supplier, or a very intense flu epidemic). And while everyone thinks first about negative events, positive forces such as an unexpected increase in demand or a new business opportunity can also put high pressure on supply chains and force companies to react.
A supply chain is considered resilient if it can resist those external forces as efficiently as possible, allowing processes to continue running even if the company’s business conditions change. Therefore, superior supply chain resilience represents a significant competitive advantage in highly volatile times. Consequently, many companies are putting supply chain resilience at the top of their agenda. But increasing resilience is challenging, and starting this process may seem overwhelming due to the abundance of factors to consider. Among these factors are:
- Scope and system boundaries that need to be analyzed (for example, strategic versus operational versus tactical)
- The type of analysis required (such as analyzing historic data versus stakeholder interviews)
- The desired outcome (such as a list of challenges versus a ranking of the effects of potential measures)
- Creating a reasonable road map to achieve the desired supply chain state
Often, companies know that they want and need to do something to improve resilience but are not sure how. My purpose in this blog post is to share insights from past and current customer projects that are important in increasing resilience, and to make you aware of an out-of-the-box service offering and methodology from SAP to support customers on this journey.
The insights are derived from a series of interviews with experienced SAP colleagues working globally for customers from different industries. The interviews were collected in collaboration with a master’s thesis student (shoutout to Roman Reuther, as well as Jasmina Müller and Kai Hoberg, all from the Kühne Logistics University). Three key insights emerge:
- Do not just optimize – rethink supply chains.
- Do not think in specific software solutions – think in terms of end-to-end processes.
- Do not enforce resilience – collaborate with your partners.
The following three sections outline the background of these insights, while the last section introduces SAP’s approach to and methodology for putting these insights into practice.
Insight 1: Do not just optimize – rethink supply chains
One aspect that came up in many of our interviews was the significance of the effects of current changes of industry dynamics and best practices. For instance, experts from the automotive industry highlighted that the “Tesla business model,” in which the car dealers are skipped and the customers are directly supplied, is increasingly popular. The obvious idea is that manufacturers can skim the dealers’ margins. Similarly, a huge shift toward vertical integration can be seen in the context of e-mobility, in which the whole end-to-end process is sometimes integrated into the OEM’s supply chain, enhancing control over its own business activities. However, this also leads to a more diversified system landscape and the need to build up additional capabilities that are completely new to OEMs. For example, an OEM with a very diversified set of discrete manufacturing capabilities may need to acquire process industry knowledge and capabilities once it starts producing battery cells. (The processes around cutting a couple of kilometer-long copper foils are quite similar to the processes used in a steel mill, where large batches of iron are processed and aspects such as traceability and serialization are central.)
We know from recent global events that supply chains need to become dynamic and agile under stress. The pandemic, plant shutdowns, lockdowns in global transportation hubs, and the war in Ukraine push toward more local-to-local supply chains. Authorities have been incentivizing this reshoring of traditionally outsourced supply chain segments – an example being the U.S. CHIPS and Science Act. However, it has to be mentioned that companies such as Goldman Sachs or Kearney were not able to quantitively prove this trend in 2021, though Goldman Sachs acknowledges that people talk about reshoring much more than before, and that it may take a while for trends like this to manifest.
Additionally, sustainability-motivated trends, such as recognizing the importance of recycling and circular economy, increase complexity but offer large potential to gain competitive advantages in the long run (especially in our current times of skyrocketing raw material prices). Some trends will likely even increase as more regulations such as the global Supply Chain Act appear on the horizon.
Consequently, it is not sufficient to simply improve a supply chain and established procedures – it is necessary to redesign and rethink supply chains. A resilient supply chain always needs to be sustainable, in line with global trends and therefore account for the zeitgeist.
Insight 2: Do not think in specific software solutions – think in terms of end-to-end processes
Many colleagues told us that during the turbulent times at the start of the COVID-19 pandemic, IT solutions were among the first parts of a supply chain that were put to the test. While companies usually have dedicated software solutions to ensure that their core processes run as smoothly as possible, the lack of well-defined end-to-end processes caused many issues. While simple workarounds, manual connections between systems, or semiautomated interfaces may have been sufficient to operate before the crisis, they became a pitfall once unprecedented dynamics put pressure on the whole IT system, and there was no time to build work-arounds.
One colleague even reported that production planning at his former company, which did not operate with a single source of truth, shifted to Microsoft Excel spreadsheets once resources and staff became sparse and the data input from auxiliary systems was unreliable. Obviously, the flow of data and the lack of synchronization with the other software solutions became a problem right away; people started working outside of systems, a lot of time and effort was lost on data preparation and cleansing, and errors in decision-making increased significantly.
On the other hand, multiple companies we heard from stated that the agility provided by a centralized and well-integrated ERP system was the single most important advantage during the COVID-19 crisis. The real-time transparency allowed them to directly react to a disruption – without losing time to check the data validity in the system.
A supply chain IT-architecture is only as strong as its weakest link. Often, the weakest link is the link itself – in terms of either data compatibility or synchronization with a system outside of the core. Please don’t get me wrong: a supply chain can’t be resilient without sophisticated tools and algorithms maneuvering the different segments through the ups and downs of a crisis (see, for instance, a blog post on improving accuracy and planning, utilizing alerts from SAP Business Network and the SAP Integrated Business Planning for Supply Chain solution). The point is that the definition of a smart portfolio and integrated network of solutions is key. Understanding the end-to-end processes, the required capabilities throughout the processes, and the enabling IT architecture to meet changing scenarios is crucial to enabling resilience.
Insight 3: Do not enforce resilience – collaborate with your partners
The third insight that was emphasized by SAP colleagues was the growing importance of collaboration and data exchange throughout supply chains.
The turbulence of the last few years changed the way companies manage and plan their supply chains. A couple of years ago, companies rolled out sophisticated planning approaches to make the supply chain as lean as possible, reduce cost, and increase efficiency. However, the crises of the past changed this significantly since companies started building up stocks to hedge against supply shortages and global market disruptions. Therefore, in some industries such as specialized manufacturing, inventory levels of up to two years were (and still are) not that uncommon anymore. Needless to say, this comes not only with an abundance of agility but also with vast amounts of bound capital. Though I acknowledge that one can imagine many cases where a large strategic buffer makes sense, a strategy of “buying what we get so that we’ll have it in case we need it” is neither efficient nor resilient, and increases turbulence in the markets even more (most prominently due to effects such as the bullwhip, which increases stocks and results in higher overall costs).
Instead, the focus should be on resilient supply management, which includes strong bilateral collaboration with existing suppliers and special attention to the agility necessary to onboard new suppliers quickly. Consequently, it’s highly recommended to promote or build strong collaboration networks with existing suppliers, and to be able to onboard and scale new suppliers who can deliver and provide buffer in times of challenge.
The benefits of close relationships and information exchange with suppliers and customers are obvious – for example, the usefulness of consistent and accurate data or automated alerts in case of delays. However, data and knowledge exchange requires strong trust between the business partners, which usually takes years of working together to build up. In contrast, in cases of an asymmetry of power, the partner with more power may enforce “collaboration rules” on the partner with less power. While this may be the easiest approach for big players, the partner with less power usually benefits far less from the collaboration and will likely try to reduce the amount of collaboration to the bare minimum. This is why both sides need to benefit from the collaboration and bring their knowledge and capabilities into the partnership. Using standardized collaboration processes and networks can help significantly reduce the effort to establish collaboration and enable data integration seamlessly and fast.
This is closely related to the second component of resilient supply management, the simplicity of the supplier onboarding process, which is often either forgotten or simply considered as a challenge impossible to improve. Of course, onboarding of a new supplier always comes along with mandatory process steps and requires some type of bureaucracy to ensure the new supplier fulfills quality and compliance requirements. Nevertheless, when critical goods became scarce, companies were somehow able to rapidly onboard new suppliers that could provide these goods. Very often, this happened at the cost of extremely great effort and time pressure on both sides (to check certificates, plan new transport routes, quality checks, and more).
Thinking about ways to improve this process, it is important to keep in mind that your company will not be the only one contacting the supplier. A new supplier will likely have the privilege of choosing to deliver the goods to the highest bidder, and having to go through extensive bureaucracy may be considered an impediment to doing business.
While going through individual onboarding procedures takes a lot of effort, standardization can become a game changer. First, because suppliers do not need to upload and reformat files and documentation to fulfill a specific customer’s formatting requirements – either on short notice or prior to a disruption in a pool of potential suppliers. Second, because new customer-supplier relationships can be set up extremely fast and end to end, from the identification of a new supplier through to goods arriving at the customer’s site.
In conclusion, the agility to start new business relationships as well as close collaboration is key. Instead of enforcing your own regulations and processes, you can increase resilience significantly by trusting in your partners and building inclusive business networks.
How can SAP support you on your journey toward higher supply chain resilience?
As I’ve discussed, there are many opportunities available to improve supply chain resilience, and many mistakes to avoid when operating supply chains through times of crisis. And there are many different ways SAP can accompany customers on their journey toward superior resilience. For instance, solution experts and architects are happy to support you in using the full power of dedicated supply chain solutions such as SAP Integrated Business Planning, SAP Transportation Management, or SAP Extended Warehouse Management, or specific applications built on SAP Business Technology Platform. Additionally, SAP Business Network offers access to an inclusive network of impactful partners.
SAP also offers a team of experienced management consultants equipped with a dedicated assessment methodology to support you. Building upon your resilience business priorities and the maturity of your supply chain’s resilience, which are analyzed in the first phase of the assessment, they can help design a software-agnostic target supply chain architecture (from an IT and business processes perspective). Then a draft for a road map that gets you where you want to go will be developed and discussed. At that point, your company is ready to start its business transformation toward greater resilience.

Reference from How to Make Supply Chains more Resilient?https://www.sap.com/documents/2023/06/b2bf65e4-797e-0010-bca6-c68f7e60039b.html
Knowledge exchange across SAP is unique, and there is an immense sense of pride in being part of a team that focuses on resilience challenges. Our goal is to build and support strong supply chains with the applications, services, and platforms offered by SAP and its ecosystem. Consequently, sharing knowledge (like in this blog post), as well as supporting customers with the approach highlighted above contributes to our corporate strategy of making the world’s supply chains more resilient. Helping the world run better in challenging times has never been more important. Feel free to follow my account to keep updated on upcoming posts or send a message if you would like to learn more about our approach and discuss supply chain resilience.
Recommend
About Joyk
Aggregate valuable and interesting links.
Joyk means Joy of geeK