

BMW kicks the tires on digital twins to drive electrification.
source link: https://diginomica.com/bmw-kicks-tires-digital-twins-drive-electrification
Go to the source link to view the article. You can view the picture content, updated content and better typesetting reading experience. If the link is broken, please click the button below to view the snapshot at that time.
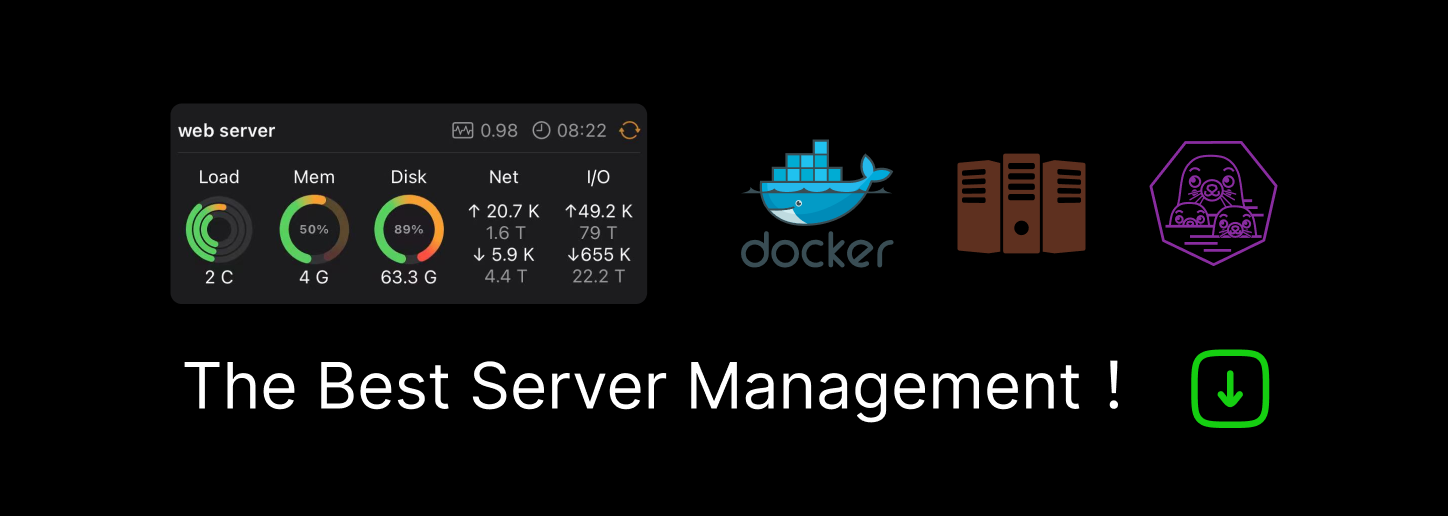
BMW kicks the tires on digital twins to drive electrification.

Regulators worldwide are pushing vehicle makers to electrify their fleets to meet sustainability goals. This won’t come cheap. Ford recently expects to lose $3 billion as it ramps up just three electric vehicle lines. The $3 trillion auto industry must grapple with electrifying hundreds of lines as they build an estimated 300 factories to manufacture 200 million electric vehicles by 2030.
At the NVIDIA GTC conference, several leading car companies announced work on digital twins programs to help lower these costs, including BMW, Mercedes Benz, Geely Lotus, Jaguar Land Rover, Rimac, and BYD.
BMW is perhaps one of the most aggressive with plans to build an entire factory digitally that will go live in 2025 in Debrecen, Hungary. A crucial part of its strategy is using the Universal Scene Description Language to create interoperability between different CAD, construction, and factory layout apps from Siemens, Autodesk, and Bentley.
It’s also building its own internal Factory Explorer app to customize the user experience for factory planning teams involved in finding, constructing, navigating, and analyzing factory data. In addition, it is working with Idealworks to simulate factory layouts for training mobile factory robots tasked with moving parts and assemblies around factory floors. Idealworks spun out of BMW in 2015 to improve autonomous goods workflows.
For decades, BMW has been using PLM and design tools to build better cars. The new digital twin capabilities will also allow them to bring considerations about the factory into planning processes. Janne Strauss-Ehrl, Project Leader for NVIDIA Omniverse at BMW Group, explains:
Our focus within the virtual factory is on the production system as a whole. Therefore, we are not so much concerned about PLM and design tools. However, when it comes to the production process, there are still several use cases that couldn’t be tackled before. E.g., it is possible to do visual inspections of parts very similar to how it is done in the real world. With the use of AI, it is even possible to detect and evaluate flaws on the surface before an actual part has ever been run off the press. It is also possible now to validate the assembly process in combination with human simulation. That way, we optimize the line setup before the hardware is bolted to the floor.
We can validate if safety margins are maintained where parts must be moved, and humans are involved. This eliminates costly reorganization after a production system has been built in real life. So, even if the virtual factory doesn’t revolutionize the car’s design process, we can still say that we help improve the return on capital employed when setting up the whole production system.
Breaking ground on the virtual factory
The biggest challenge goes into setting up the virtual factory. BMW has experts in each facility that uses NVIDIA Omniverse. Today they are focused on planning, but Strauss-Ehrl expects to move to a whole new level once shop floor data is also integrated into the platform. This will enable them to move from a virtual image of the factory to a “living organism.”
The improved interoperability alone has allowed the planning team to detect, discuss and enhance critical situations more effectively. Previously they worked across different tools that did not provide the same level of detail and transparency that they now expect with a consolidated digital twin connected by USD. Annotations in one tool can be surfaces across all the tools in the ecosystem.
BMW is working with NVIDIA to bring helpful functions into its tools and improve usability. Strauss-Ehrl considers this a work in progress towards a full digital twin. They are also working with a development and operations provider that is helping them develop BMW Group specific enhancements. They are running everything on-premise in a private data center in the pilot phase but plan to transition the infrastructure to the cloud to scale as needed for productive use.
NVIDIA channel partners also play a valuable role in providing equipment, services, and licenses. BMW is also building a team of technical experts as part of its internal DevOps to keep the machine running, fine-tune them, and develop improvements.
An evolutionary process
BMW has been kicking the tires of digital twins technology in smaller pockets. This newer effort will help unify coordination across different groups. Strauss-Ehrl says:
Currently, we are in an early stage of harvesting the benefits of digital twins. There have been digital twin scenarios before, mostly focusing on robot simulation. These simulations are done in specialized tools and are usually restricted to small cells. For the Debrecen use case, we have taken the simulations from the specialized tools and embedded them into the virtual factory. This enables us to validate the situation comprehensively and also to check transitions from one cell to another, which has not been possible before.
By combining the best of two worlds, we can identify trouble in a very early phase and thus reduce modifications to hardware later on. This not only applies to greenfield but also to brownfield projects where new hardware is brought into existing structures. Since for such projects, we can not only rely on planning data but also on point clouds from 3D scans of the facility, we can even detect errors in the planning data if, e.g., pillars or ceilings in the real world are not exactly at the position as the drawing would suggest. In surroundings where space is limited, a few centimeters, give or take, can be decisive if a machine can be fitted or not.
An object orientation
Digital twins also bring an object-oriented approach that allows people to think about things as connected hierarchies of objects. These same ideas transformed software development with programming languages like LISP that later got incorporated into COBOL, C++, and Java. An object-oriented approach makes reusing, combining, and fine-tuning things like conveyor systems, work cells, or electrical infrastructure easier. This allows BMW to align digital planning with how humans are used to thinking. Strauss-Ehrl argues:
The way digital models of vehicles are created has not changed so much yet. However, the process for creating the layout and other asset data is transforming. To make everything useful in a digital twin scenario, all data must be object-oriented so that they can communicate with each other and signals can be brought to the right objects. Current planning software does not always support the object orientation. When introducing assets into the virtual factory, crucial information is stored in the USD files that will enable us to really fire up a digital twin so that objects not only know that there is some piece of geometry adjacent to them but also what this piece of geometry is, what data it consumes, where it is connected to, what parts it consists of, if there are enough spare parts in stock and many other things.
However, getting their existing data into the USD digital twin format is still a work in progress. USD started out just describing the look of things for making movies, and NVIDIA has been adding new capabilities for describing how they work. Strauss-Ehrl explains:
Right now, the conversion process from proprietary file formats to the USD format is still a challenge. Especially when standards of the proprietary file formats change as the software evolves and the converters are not able to interpret the changes right away. There will always be the need for specialized tools that are targeting very specific use cases. In order to bring everything into one common platform, there will, in turn, always be the need for converters. We are also working closely with NVIDIA in getting converters that are capable of transforming data with the highest possible quality. We believe this is also a key issue to maintain the value of the platform for an industry target group.
The USD file format is a very powerful one. It would be very beneficial if there would be an industry standard on how to use it so that components and data flows can be connected more easily. Right now, this is a very sophisticated process that needs to be set up. When operating in the virtual world, the amount of data that needs to be handled can be enormous, depending on the size of your scene. Once live data from shop floor systems also comes into play, this amount grows even more. I guess there will be a great demand to handle the throughput of data even more efficiently as today to make the best use of digital twins.
My take
Efforts to bring digital transformation to physical products will require harmonizing digital representations of the real world. NVIDIA’s efforts to build tools to process USD more efficiently show tremendous promise as a middle tier for staging data from different tools and capture processes. But it is still a work in progress as enterprises look to represent complicated things like factory processes better.
There will also be a growing role for digital twin channel partners to organize the licenses and equipment for realizing these new tools. This means high-end hardware for enterprise data centers, new cloud services, high-performance workstations, video collaboration spaces, and eventually head-mounted displays and augmented reality gear for front-line workers. It is telling that even though BMW is collaborating closely with NVIDIA on improving the underlying technology, its channel partners are still providing the licenses and facilitating the delivery of the physical hardware required to simplify and scale the business side of these efforts.
Recommend
About Joyk
Aggregate valuable and interesting links.
Joyk means Joy of geeK