

No Magnets, Big Power: BMW’s Fifth-Generation Electric Motor (2022)
source link: https://www.motortrend.com/news/bmw-ix-m60-brushed-electric-motor-tech-deep-dive/
Go to the source link to view the article. You can view the picture content, updated content and better typesetting reading experience. If the link is broken, please click the button below to view the snapshot at that time.
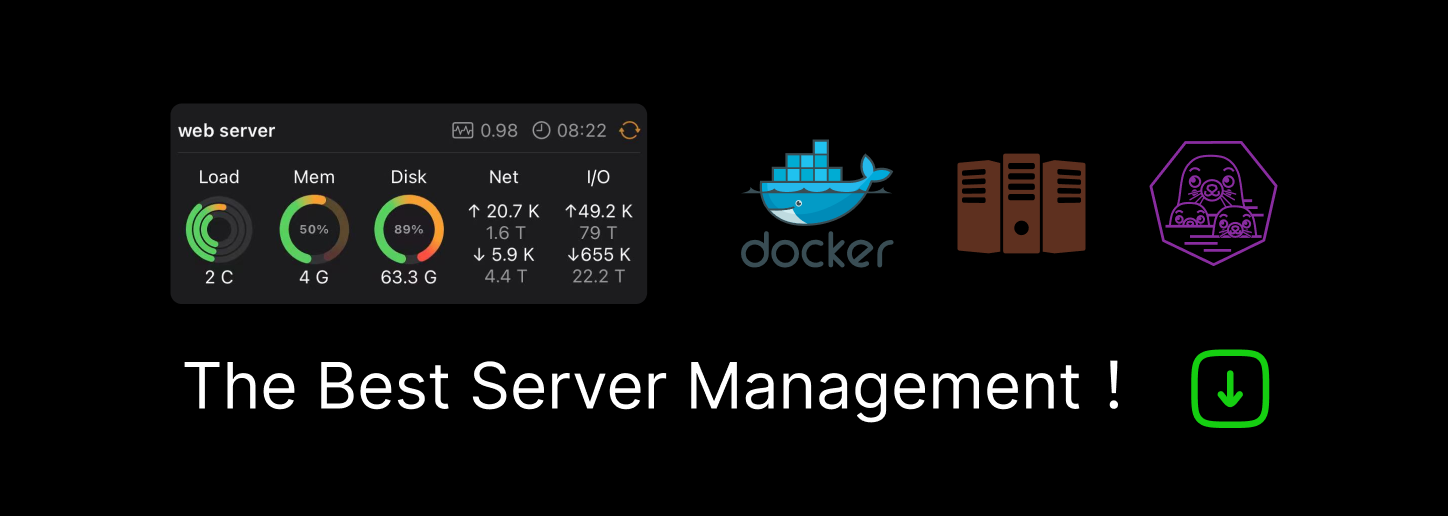
We've hinted at the impressive power output of the BMW iX M60 motor in our First Look, but its fifth-generation electric motor technology deserves its own examination. That's because it's both extremely high-tech and a little bit old-school. Here's what you need to know, and why it's so interesting that BMW used this motor on the iX M60. It's a big advance in terms of the efficiency of the electric motor, while getting away from the use of rare earth minerals.
The Electric Motor
Before we dive in any further, if you're not familiar with the different types of EV motors used in vehicles, we have a thorough E-Motor 101 course. Feel free to open that in another tab and use it as a reference. But all electric motors rely on the properties of electromagnetism to convert electricity into torque to drive the vehicle. One pole of a magnet being attracted to the opposite pole of another, and like poles repelling each other, is what drives an electric motor. An easy approach is to use strong permanent magnets in the spinning part of the motor called the rotor, and an electromagnet (conductive wires wound around a ferromagnetic material) in the stationary "can" it spins in, which is called the stator. Reversing the electric polarity in the electromagnet reverses the magnetic polarity, and it's this switching that pulls the permanent magnets around. But the rare-earth materials that make permanent magnets are getting hard to find, so BMW is getting away from them by using electromagnets in both the stationary stator and the spinning rotor. It's relying on an old technology—brushed motors—to make this possible.
Turning It Old School, EV-wise
If you play with radio-controlled rock crawlers or have taken apart your electric drill, you're familiar with brushed motors. These have been around since the invention of the electric motor and are called "brushed" because a set of brushes transmit electricity to the spinning rotor via what's called a commutator on the rotor. The rotor's electromagnetic windings are energized by the commutator. As power is applied, electromagnetic forces are created in both the stator and rotor, switching them both in such a way as to make the rotor spin. Increasing the switching speed within the electromagnets and increasing the current causes the speed to increase.
The rotor can include two or many more electromagnetic fields, each energized by a pair of contacts (and brushes) on the commutator. Likewise, the motor uses as few as two brushes, but can use as many brushes as necessary to achieve the design goals. Brushes can be made of nearly any material, just so long as you can pass a current through it. In many cases, these brushes are sintered from powdered metals and other materials, much like your brake pads are. Even how the brush faces are grooved can affect performance, just as with brake pads. And like your brake pads, the brushes and commutator generate dust and wear out, requiring periodic replacement, which are some of the reasons these are not currently used in any modern EVs or hybrids.
Brushless Motors
Which brings us to the majority of the motors you see on the road today. Brushless motors either utilize permanent magnets in the component that spins, or they "induce" a magnetic field in a winding wrapped around a ferromagnetic material in the spinning component. The latter type is known as an asynchronous AC induction motor, and it's what most Teslas started out using.
The biggest takeaway from this is that brushless motors are preferred over brushed because they do away with the maintenance and dust that come with brushes rubbing a wearing surface (the commutator), both of which increase the lifespan of the motor. Disadvantages are higher initial cost and more complicated motor speed controllers that typically require three Hall-effect sensors to properly measure the positioning of the stator and rotor (although some modern controllers have found clever ways to do without these sensors).
The Fifth-Generation BMW Electric Motor
This fifth-generation BMW motor has no magnets. It operates as a three-phase AC synchronous motor using brushes and a commutator to provide power to the rotor windings, meaning that AC brushed motors aren't just for third-world electric locomotives any more.
We asked BMW about the life expectancy of those brushes and commutators, and what happens to the dust as they wear. While they couldn't give us a lifetime estimate for the brushes, they did reassure us that the brush modules are "in an enclosed and sealed compartment, eliminating dust contamination inside the stator/rotor wiring." Anyone who has worked with brakes or even brushed DC motors knows just how fine those dust particles are. It will be interesting to see both how long they last and just how much dust those modules will actually contain (or release).
The Case Against Using Magnets
Permanent magnet machines typically rank as the most power-dense electric motors, but there's no turning permanent magnets "off. " Their magnetic fields never change, so when they're not being powered by energy in the stator winding, they're generating energy in those windings, which creates drag. This is why some EVs powered by multiple motors either use a clutch to decouple and idle a permanent-magnet motor when it's not needed, or they fit one asynchronous AC induction motor (which suffers no such losses) and one permanent-magnet motor. The rare earth metals that comprise permanent magnets are also increasingly hard to source ethically, with China controlling most of the rare-earth reserves, all of which is driving BMW and other motor manufacturers to look for other ways to make power-dense electric motors.
The Case For BMW's Brushed Motor
According to BMW, this fifth-generation motor system allows for more energy density, faster switching frequency, and better heat management. "All of which," says BMW, "translates to higher RPM, more torque, and even more power." BMW is betting that modern materials and sealing technology will allow modern-day brushes and commutators to last for a reasonable service interval in the life of a modern EV.
From the looks of it, BMW isn't exaggerating about output. Indeed, the standard combined output of both the front and rear motor of the iX M60 is 532 hp and 749 lb-ft of torque. Individually, the front motor provides 255 hp while the rear motor provides 483 hp in normal operation. In Sport Boost mode, that jumps to a combined 610 hp while Launch Mode should slam you in the back of your seat with 811 lb-ft of torque, combined. All without a change in battery power and in a package that gives you much deeper tunability of the motor.
It's clear that the battle for magnet-less motor supremacy is only just getting started, and BMW is answering a key criticism frequently leveled against EVs: relying on rare, sometimes unethically mined materials makes EVs worse for the planet. We're truly stepping into an interesting time in electric motor development.
Recommend
About Joyk
Aggregate valuable and interesting links.
Joyk means Joy of geeK