

难逃“膜”咒:谁卡了电池的脖子?
source link: https://www.qianzhan.com/analyst/detail/329/221212-59b63b0b.html
Go to the source link to view the article. You can view the picture content, updated content and better typesetting reading experience. If the link is broken, please click the button below to view the snapshot at that time.
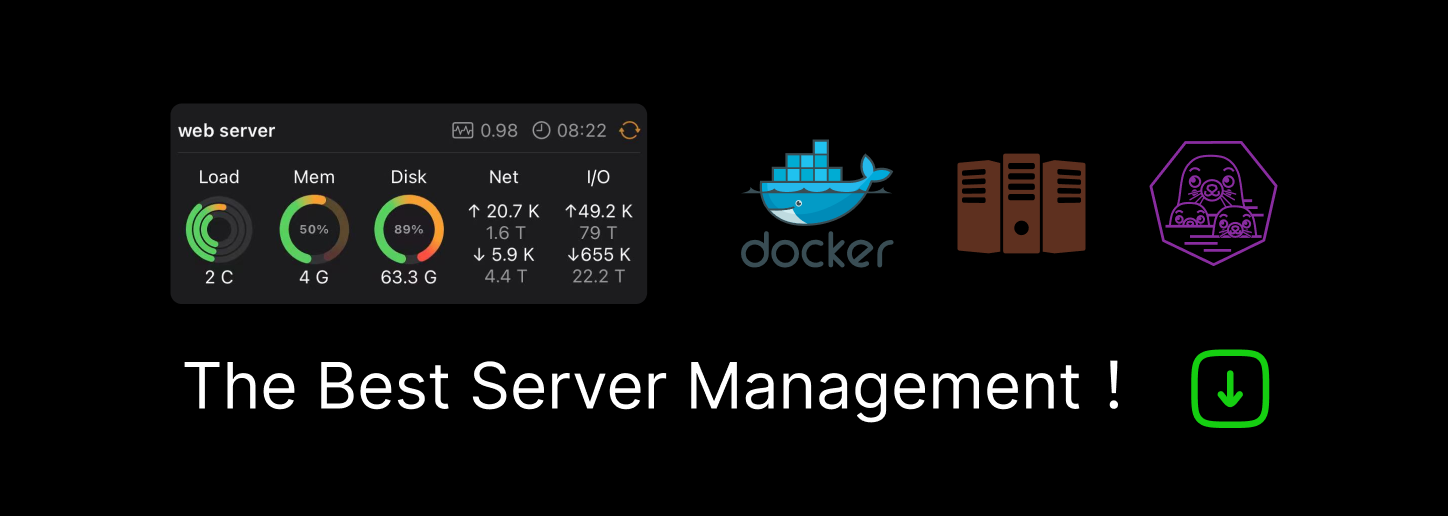
难逃“膜”咒:谁卡了电池的脖子?
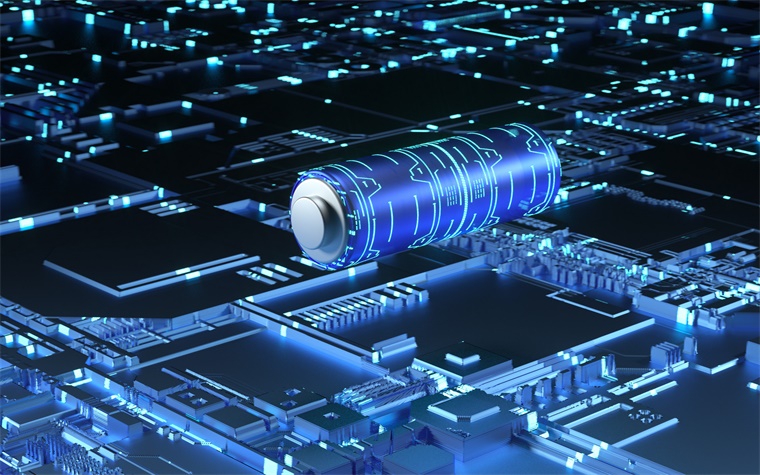
(图片来源:摄图网)
作者|常心悦 来源|芯流智库(ID:xinliuzhiku)
在电池行业中,有一张膜至关重要,那就是质子交换膜。
在氢燃料电池与液流电池如火如荼的发展态势下,质子交换膜作为其中的核心材料,也搭上了行业成长的顺风车。
然而,正如芯片之于电子行业,质子交换膜也紧紧地“扼住了电池的咽喉”。长期以来,国内相关产品都不得不依赖进口,量少且价高,可谓是“千金难买一膜”。
这是因为,要造出这张薄薄的膜,工艺难和成本高是横在国内选手面前难以渡过的湍流。
那么,质子交换膜要如何走出一条国产替代之路?国产膜何时能够成为支撑电池行业的中流砥柱?
本文将分以下三个部分,分析质子交换膜的技术难点与市场痛点,并提出国产化的破局点:
一、电池的“芯片”;
二、氢能与储能的机遇;
三、国产化出路在何方?
一
电池的“芯片”
质子交换膜,顾名思义,是用作正负极间质子(氢离子)交换的场所,它的特异功能是可以让质子选择性透过,从而保证电极之间的离子交换顺利完成,最终完成电池的功能。同时,质子交换膜也对正负极的电解液进行隔绝,避免交叉污染。
这片薄薄的聚合物膜的发明,源自于人们对清洁能源的不懈追求。早在1800年,英国化学家提出电解水可以制氢。几十年后,第一个氢燃料电池诞生。
到了20世纪50年代末,美国通用电气公司将铂作为催化剂沉积在膜上,研发了质子交换膜燃料电池,用于NASA的太空任务。
最早的质子交换膜是聚苯甲醛磺酸膜,这种材料在干燥条件下易开裂。此后研制的聚苯乙烯磺酸膜(PSSA),能够在干湿状态下都保持较好的机械稳定性。
20世纪60年代,美国杜邦公司开发了全氟磺酸(PFSA)膜,即Nafion系列产品。
这一产品可以说是质子交换膜发展史上的里程碑,其凭借着优异的化学稳定性、高机械强度,以及在低温和高湿度下突出的离子电导率,大大提升了燃料电池的性能和使用寿命,同时还能降低催化剂成本。
此后,质子交换膜从实验室走向了商业化,在氯碱工业、燃料电池、液流电池等领域得到广泛应用,越来越多的入局者相继开发了多种技术路线,相关的论文和专利数量迅速增加。
目前根据含氟情况分类,质子交换膜主要包括全氟磺酸质子交换膜、部分氟化质子交换膜、非氟化质子交换膜、复合质子交换膜。其中大部分仍处在研究阶段,市场上应用最为广泛的仍然是全氟磺酸膜。
继杜邦公司以后,日本的旭硝子公司(Asahi Glass)、旭化成公司(Asahi Chemicals),美国的道化学公司(Dow),加拿大的巴拉德公司(Ballard),比利时的苏威公司(Solvay),相继开发出不同结构的全氟磺酸膜,这几家公司也成为了质子交换膜领域的巨头。
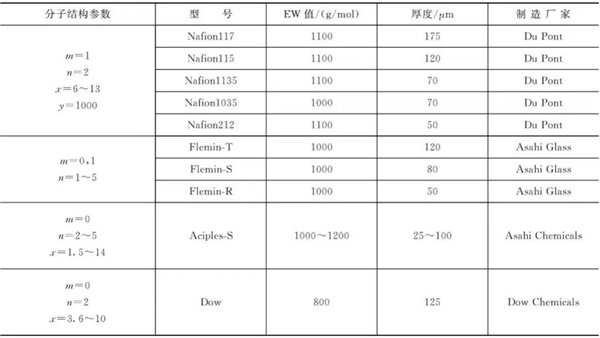
商业化全氟磺酸膜的特征参数
(注:EW值表示含1mol磺酸基团的树脂质量)
全氟磺酸膜被称为氟化工产业链的技术难度巅峰。那么,全氟磺酸膜的工艺难点究竟在哪里?
从制备过程来看,困难主要来自四个环节:原材料PSVE单体的制备、四氟乙烯的获取、树脂的聚合和成膜。
PSVE单体,即全氟磺酰基乙烯基醚,其制备反应条件十分严苛。为了规避技术纠纷,各厂家领先开发出不同结构的PSVE单体后纷纷申请专利,因此这一环节专利保护性较强。
四氟乙烯是制作全氟磺酸树脂的核心原材料,具有易爆炸特点,运输难度大,因此生产全氟磺酸膜的企业,一般需要具备四氟乙烯的自供能力。
树脂的聚合与成膜过程,存在着机械强度难以保证、产品平整度和厚度难以取舍的问题,使其满足工业化生产规模具备相当大的技术难度。
质子交换膜的高工艺壁垒,使产品从一出生就被打上了“制作难”“价格高”的标签,主流的技术也已经被国外抢跑。那么,国内玩家还能否拿到入局的门票呢?
答案藏在中国的能源革命。
二
氢能与储能的机遇
只要掌握了能源,往往就有了引领世界发展的话语权。
300年前,煤炭时代下的英国用蒸汽机缔造了日不落的神话。150年前,电气时代下的美国凭借着对石油、天然气资源的掌控,成为了世界霸主。
能源世界发展到现在,下一个阶段的命脉将是清洁能源。而这一把开启新时代的钥匙,掌握在中国手里。
在双碳目标的驱动下,中国在清洁能源设备制造、产能、输送等环节均跑到了世界领先的位置,能源结构正在快速进行“清洁替代”、“电能替代”。
在这个进程中,可再生能源消纳所存在的随机与波动性,带来了大量的弃风、弃光、弃水等现象。要解决弃电问题,能源市场将目光投向了氢能和储能。
中国将成为全球最大的氢气生产国和消费国。
在生产端,由于煤制氢和工业副产氢的污染程度较大,目前各国都在大力发展电解水制氢技术。
在消费端,《中国氢能源及燃料电池产业白皮书2020》(本文简称“白皮书”)预计,2030年碳达峰情景下,我国氢气的年需求量将达到3715万吨,在终端能源消费中占比约为5%。
这么多氢气怎么生产?其实,那些消纳不了的风光弃电正好能够派上用武之地。按照2020年三电弃电量520亿千瓦时计算,可产生116万吨氢气,部署电解槽装机量需求为18.6GW。
目前弃电制氢技术尚未成熟,规模较小,与其他制氢路径相比缺少成本优势。随着可再生能源电价下降、质子交换膜电解装置成本下降,《白皮书》指出,可再生能源制氢成本有望在2030年实现平价上电网。
风光发电快速发展的背景板上,储能也是一颗冉冉升起的巨星。在多种技术路径中,液流电池凭借着安全性高、使用寿命长等优势突围而出。
质子交换膜正是构建液流电池结构的重要部件。以目前最为成熟的全钒液流电池为例,其电池反应式为:
阳极:VO2+ +HO == VO2+ + 2H+ + e-
阴极:V3+ + e- == V2+
总反应:VO2+ + HO + V3+ == VO2+ + 2H+ + V2+
通过质子交换膜的传导,两极反应中的质子才能构成完整的回路。

数据表明,我国目前全钒液流电池储能项目规模超过120MW,在建规模约110MW,按照目前建设规模计算,约耗用15-20万m2质子交换膜,在建工程完工后所耗数量还将更上一层楼。
弃电制氢、储能系统的发展,均离不开质子交换膜。能源革命的战略重任,这张薄薄的膜承受了太多。在这个意义上看,国产质子交换膜的替代势在必行。
三
国产化出路在何方?
国产质子交换膜被海外巨头的两只手卡住了脖子,那就是技术与市场。
首先,全氟物质的合成与磺化、后续的成膜环节都有着极高的技术要求与繁琐的工艺流程。
目前工业中生产全氟磺酸质子交换膜的方法,主要是用全氟磺酸树脂通过熔融挤出法和流延法制成膜。
熔融挤出法是最早用于制备全氟磺酸膜的方法,工艺成熟、生产效率高、环境友好,但生产的膜较厚,且挤出成型的膜需要经过水解转型才能得到最终产品,而水解工艺几乎被美国和日本企业所垄断。
流延法成膜具有产品更薄、性能更好的优势。杜邦的Nafion系列中,用于储能方面的膜主要是采用流延法生产的NR211和NR212,其厚度分别为25.4微米和50.8微米,而采用挤出法生产的N115和N117,其厚度分别为125微米和183微米。
但流延法工序长、流程复杂,且其中使用的有机溶剂回收难度较大。目前国产全氟磺酸膜龙头东岳集团和苏州科润采用的是钢带流延法,其产品性能与国外同类竞品仍有一定差距。
根据德温特创新数据库的数据,日本质子交换膜专利数量达到全球50%,而中国相关专利只占10%左右,国内企业往往需要依赖专利授权切入质子交换膜领域。
其次,居于电池“心脏”地位的质子交换膜,对于膜厚度、化学稳定性、质子传导率等性能指标有着高要求,先发企业通过验证进入正式产线后,就牢牢粘住了客户。高替换成本使得后来者难以居上。
国产膜的普遍厚度只能做到15微米。国电投氢能公司能够生产8微米的质子交换膜,但距离大规模量产仍有较大距离。而美国戈尔在杜邦Nafion膜基础上生产出的增强型Select膜,最薄可达5微米,其8微米膜已经实现量产。
截至2019年,戈尔的质子交换膜为大部分国内膜电极生产厂商使用,市场份额高达90%以上。面对高度集中的市场格局,国内玩家目前只能打价格牌,以较国外低30%-40%的售价争取生存空间。
低价倾销策略在高端局终归走不了太远。
卡脖子的手,未尝不能变成未来质子交换膜国产化的抓手。
技术方面,国产膜可以另辟蹊径,自研其他技术路径。主流的全氟磺酸膜存在尺寸稳定性差、燃料渗透率高等问题,且高昂的价格一定程度上限制了全钒液流电池的产品化和工业化。
非氟离子交换膜具有广泛而廉价的材料来源。在国家支持下,中国科学院大连物化所和大连融科研发团队研究开发了非氟离子交换膜材料,实现了非氟膜材料自主化小批量生产。
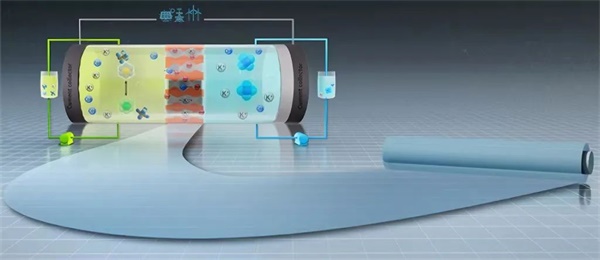
大连化物所开发出高性能、低成本碱性体系液流电池用膜材料
市场方面,国产质子交换膜可以借鉴锂电隔膜的发展经验,团结产业链力量、降低成本。
锂电池隔膜行业中,湿法设备严重依赖进口,限制了产能扩张,也给企业带来了高额设备投资负担。目前隔膜企业一边大力采购海外设备,另一边也在积极推动国产设备进口替代进程。
此外,锂电池隔膜企业还通过一体化来降低生产成本,并控制产品质量。伴随着涂覆膜需求的增长,越来越多的隔膜龙头开始自建产线,生产出基膜后直接进行涂覆,大大提高了品控效率和盈利空间。
向上推动生产设备国产化,向下垂直进行一体化,可能会让国产高性能质子交换膜大规模量产的那一天,更早地到来。
尾声
汉朝出土的金缕玉衣,薄如蝉翼,却价值连城。
几千年后,同样轻薄却昂贵的质子交换膜,成为了国内电池行业的心魔。
在中国制造的年代,大国工匠们筑造了金碧辉煌的宫殿,撑起了领先世界的王朝。
如今中国制造2025近在眼前,第三代能源革命的发令枪口正冒出硝烟。这一次决定领先者的,将是对高新技术的不懈攻关,和产业力量的众志成城。
质子交换膜的技术突破与产业化,仍需要持续集中产学研力量,走出一条国产化的自强之路。
激流勇进,我们期待着国产电池破除“膜”咒的那一天。
编者按:本文转载自微信公众号:芯流智库(ID:xinliuzhiku),作者:常心悦
Recommend
About Joyk
Aggregate valuable and interesting links.
Joyk means Joy of geeK