

The smart and connected factory is made possible by automation
source link: https://diginomica.com/smart-and-connected-factory-made-possible-automation
Go to the source link to view the article. You can view the picture content, updated content and better typesetting reading experience. If the link is broken, please click the button below to view the snapshot at that time.
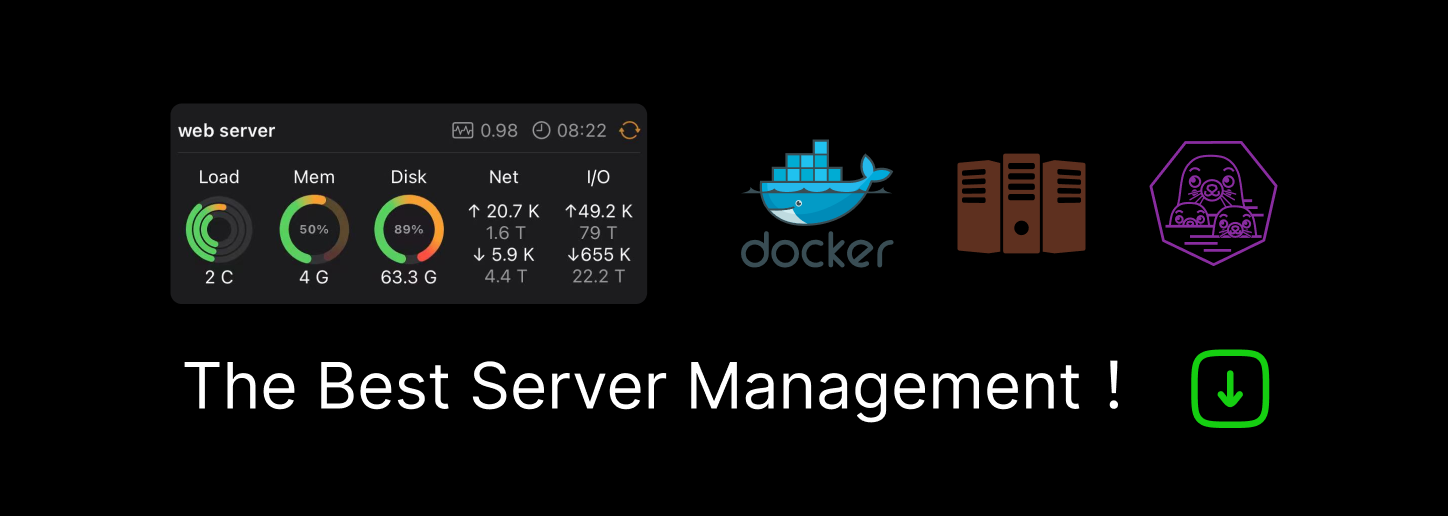
The smart and connected factory is made possible by automation

(© Gorodenkoff - Shutterstock)
The adoption of automation is one of the unexpected game-changers that the COVID-19 pandemic has accelerated in manufacturing. The impact is nowhere more robust than on the shop floor.
Manufacturers placed their factories in less-developed countries with low labor costs.They employed, and are still stuck with, a geographic footprint for production that was driven by labor arbitrage around the globe, rather than by factors such as proximity to customers or ecological considerations. In fact, supply chains expanded with goods being produced farther and farther from the customers who buy them.
But the pandemic, and several other factors, changed all that. With the amount of disruption in the past two years, happening at an accelerating pace, the only constant now is change. The need to reduce delays and transport costs, as well as the pursuit of more sustainable production have led organizations to adjust their manufacturing footprints.
What does that mean? Since the 1980’s, the global manufacturing business model has been centered around locating physical factories in countries where labor costs were cheap. That made sense when global supply chains and just in time sourcing were efficient and cost effective. Now, with shipping costs through the roof, and both containers and spots on ships hard to come by, companies are recognizing the benefit of reduced transport and moving manufacturing closer to customers - but that requires a rethink of how these factories operate.
Thankfully, the advancement of digitalization and automation, robotics, machine learning, and advances in manufacturing techniques have increased manufacturers’ ability to create smaller, more automated and much smarter factories located in countries and cities closer to the customer. Reshoring and back-shoring is picking up steam as technology helps companies reduce labor costs via automation.
Automation makes it possible
Automation is enabling manufacturers to build new smart factories in developed countries. Automation helps factories operate with far less unskilled (mainly human) resources. Less labor means less labor costs. Factories operating out of high-cost manufacturing hotspots such as Germany and Japan are largely automated for production and deploy far fewer employees, relying mostly on skilled engineers to maintain the machinery and the equipment. In addition, fully standardized, digital and automated processes can be much quicker than processes that involve human interaction and manual tasks.
Increased automation makes locating facilities in high-cost but also highly educated countries a smart move. For example, a manufacturing execution system (MES) for the coordination of production machinery can automate the task of machine maintenance scheduling. But decisions still need to be made by people who are responsible for the outcome. These human decision points stand in the way of the complete “lights-out” factory, but not in the way of progress. The more automated the factory becomes, the more flexibly it can react to market changes.
Automation is complex, and there’s a lot of work to do to lay the foundation at any facility. The most urgent question for most production companies is not how to implement the latest technology; most have pilot projects and implementations for data analytics, digital manufacturing technologies or artificial intelligence.
The key challenges are 1) how to bring all these different technologies together and 2) how to roll them out on the entire production environment. Replacing old technologies on a global scale often means a change in workflows and measurements. This change can be challenging. Standardizing operations at all production sites, being able to monitor the same key performance indicators (KPIs) in the same way, and automating well-defined processes across all operations are the first areas to address.
For example
We are seeing increased in investments in major European and US markets from companies that are returning factories closer to their largest customer bases. Procter & Gamble set up a smart factory in the Czech Republic to leverage local talent and to draw from an ecosystem of local universities and startups. Infineon and Intel, leading manufacturers of semiconductors, were among the first companies to build new factories in high-cost countries to increase access to human capital, capacity and control of engineering and design. Infineon constructed a new smart facility in Villach, Austria, and Intel built one in Atlanta in 2021.
In addition, Intel announced in May that it plans to invest another €33 billion in a European chip manufacturing facility. Other recent examples of new factory investments in Europe include General Motors, which announced on April 4 that it is investing a total of $2 billion in two manufacturing plants in Ontario, and Northvolt, which publicized its decision to place its 60 GWh Gigafactory in Europe to build lithium-ion batteries for the European market from 2025. These investments herald the promise of thousands of high-tech jobs.
Factories with more automation are complex and need workers with specialized skills, college degrees, etc., as opposed to strong backs. But it is increasingly hard to find people willing and qualified to operate a manufacturing plant in developed economies. A shortage of workers with the right skills and knowledge will drive up wages in high-cost countries even further. Whether or not higher-priced labor will negate the lower labor demands enabled by automation remains to be seen.
Will the trend continue to accelerate?
In June, Lego announced it will invest $1 billion in a new factory in Virginia. The toy company previously had a factory in Connecticut, but it closed in 2006 due to lack of demand. The new factory will be Lego’s second in North America, along with Monterrey, Mexico.
According to a Lego news release, the factory will create 1,700 jobs and feature an on-site solar park producing enough energy to supply 100 percent of the factory’s requirements.
Carsten Rasmussen, Chief Operations Officer of the LEGO Group, said:
Our factories are located close to our biggest markets, which shortens the distance our products have to travel. This allows us to rapidly respond to changing consumer demand and helps manage our carbon footprint. Our bricks are made to last for generations, so we need skilled employees trained to work with precision molding technology.
“We look forward to working with the Virginia Talent Accelerator program to help build a great team who are motivated by our mission to inspire and develop the builders of tomorrow.
Smart Factories – the future of automation and what comes next
As more and more manufacturers embrace automation, sustainable practices and the nearshoring of facilities, smart factories, which utilize not only automation but other Industry 4.0 technologies and processes, are becoming increasingly common. Infor has partnered with Deloitte to open The Smart Factory @ Wichita on the Innovation Campus of Wichita State University to help manufacturers explore use cases for new technologies and, ultimately, to transform their facilities into smart factories.
Housed in a net-zero energy building, The Smart Factory @ Wichita is powered by a renewable energy smart grid and is outfitted with wind trees, solar assets and smart lighting. It includes a fully operational production line and experiential labs for developing and exploring smart factory capabilities.
For companies interested in exploring Industry 4.0, Deloitte creates a customized visit based on that organization’s areas of interest. The experience features lab-based demonstrations, use cases brought to life, and a hands-on workshop designed to help the organization build a road map to accelerate growth.
Representatives from many manufacturing companies are expected to utilize the Smart Factory @Wichita’s 60,000-square-foot facility during the coming year. They will have access to a working production floor, where they can test drive an array of advanced manufacturing techniques, Industry 4.0 technologies and concepts, including artificial intelligence, machine learning, big data, cloud and edge applications, robotics and vision solutions.
While the Smart Factory @ Wichita only recently opened its doors to manufacturers, the collaboration between Infor, Deloitte and Wichita State already is providing them with insights on how they can drive new business models and boost quality, productivity and sustainability. Infor, Deloitte, Wichita State and the powerful Smart Factory partner ecosystem, which includes AWS, will enable manufacturers across numerous industries to accelerate their journeys to the cloud, adopt state-of-the-art Industry 4.0 technologies and, ultimately, transform their businesses.
Many companies have already begun to integrate Industry 4.0 technologies, including artificial intelligence, into their business processes.As the world’s largest manufacturer of multidirectional forklifts, Infor customer Combilift has 60,000 unique trucks in operation to meet each client’s industry-specific needs.
To help ensure that trucks, which need service, receive the right parts for the job, Combilift utilized Infor’s Coleman AI solution in combination with its Infor CloudSuite Industrial ERP system. This helped automate the process of generating the parts lists for specific jobs, improving the efficiency and accuracy of the recommendations, scaling the service quote process, reducing stress on staff and ensuring a first-time fix for clients. Kenny Gilmour, Global Parts Manager at Combilift, says:
Our global parts department relied on a knowledge-based, manual process in determining the sum of parts needed to service a truck.
This approach is not always accurate and consistent, especially with less-experienced staff. With the global staff shortages, trying to recruit staff who are already trained is, obviously, exceedingly difficult. But with Infor Coleman AI, we can train the machine and, in turn, it can train us.
In less than 60 days, recommendations were delivered directly in the Parts Estimator screen of Infor CloudSuite Industrial. This is where the parts department spends most of its day, so having these recommendations available directly in the business application generates faster, more accurate quotes with the following results:
- 30% increase in first-time fixes
- 30% faster completion of service jobs
- 30% increase in revenue per transaction
- 40% reduction in service job costs
- 75% faster time to determine related parts (from 20 minutes to 5 minutes)
- Improved customer satisfaction and referrals due to less equipment downtime
- Improved efficiency with less time training new hires
Recommend
About Joyk
Aggregate valuable and interesting links.
Joyk means Joy of geeK