

Customer Engagement for Lot Size of One (MTO scenario) with Advanced Variant Con...
source link: https://blogs.sap.com/2022/08/07/customer-engagement-for-lot-size-of-one-mto-scenario-with-advanced-variant-configuration-scope-item-55e/
Go to the source link to view the article. You can view the picture content, updated content and better typesetting reading experience. If the link is broken, please click the button below to view the snapshot at that time.
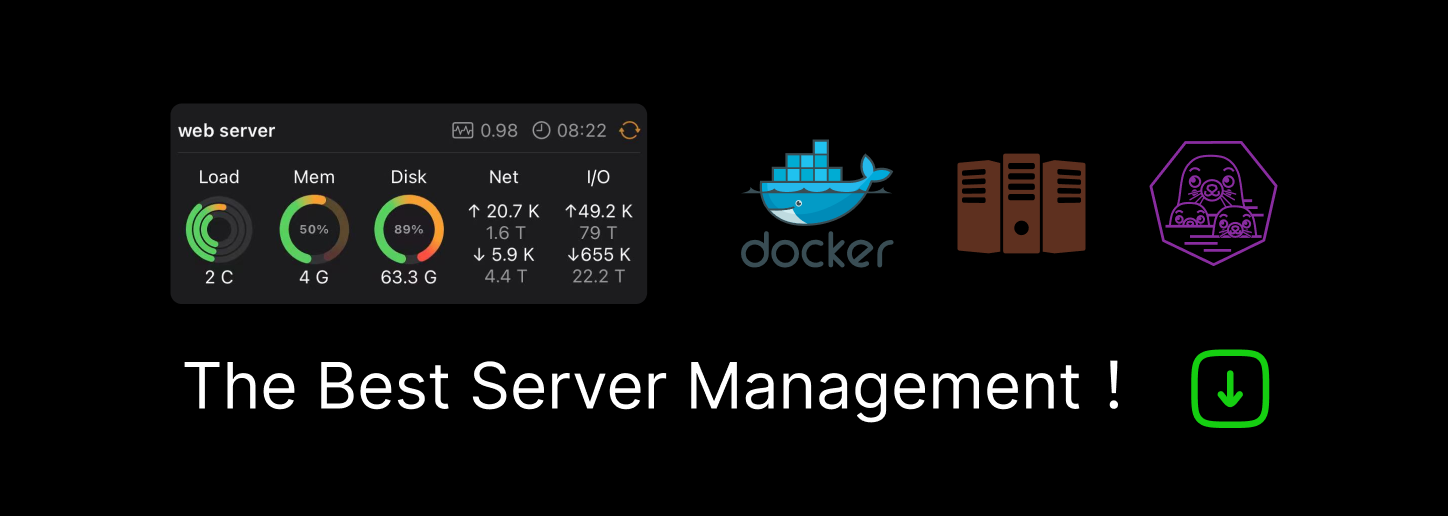
Customer Engagement for Lot Size of One (MTO scenario) with Advanced Variant Configuration | Scope Item ’55E’
Objective:
Objective of this blog is to create awareness of Scope Item – 55E and to share the experience of the recent workshop conducted with Customers and Partners to walk them through the process and evaluate whether the Best Practices outlined synergize with the actual business process at companies.
Target audience for this blog:
Any user who wish to understand the basic End-to-End Business Process of Lot Size of One (MTO usecase) or users who wish to evaluate the Best Practices defined by SAP can go through this blog for a brief understanding.
About 55E:
Scope Item 55E is designed to cater end-to-end business scenario for Lot Size of One (MTO process). The test script flows with multiple personas from receiving demand till fulfillment of request. 55E scope item was made available since S/4 HANA Cloud Edition – 2202 release.
Link to the 55E scope item: https://rapid.sap.com/bp/scopeitems/55E
Coverage of business flow with classification based on user roles (persona) will be detailed in following part of the blog.
About Customer Engagement Initiative (CEI):
Customer Engagement Initiative or what we in short refer as CEI, is a service provisioning by SAP, where the engineering / product management get to float the innovation ideas with Customer and Partners to learn their views and feedback. This engagement provides an opportunity to Customers and Partners to voice their thoughts to shape the roadmap of SAP products.
Once the topic of discussion is approved from SAP central team, then the Customers and Partners are made aware of topics via influence portal (Influence SAP Software Development) . Registered Customers and Partners are checked for the NDA (Non Disclosure Agreement) and FBA (Feedback Agreement) before participation in these workshops.
Few Customers and Partners who participated in the workshop;

Picture#1: Logos of Customers and Partners participated in the CEI program
Flow of the workshops:
- Workshop#1: Initial Call, stage setting for expectation (both sides)
- Workshop#2: Demonstration of end-to-end MTO business process flow
- Workshop#3(offline engagement): Feedback workshop via Mural board
- Workshop#4: Conclusion meet – Response to feedbacks and queries.
Brief on workshop#1:
The initial call was a ice breaker / introduction round. During the call, we from SAP pitched in the motive of the workshop and the expectation from the participants (feedback and queries)
Timelines for the workshop and brainstorming was shared for participant’s reference.

Picture#2: Timeline of the engagement model

Picture#3: Introduction call with Point of Contacts
Brief on workshop#2:
The second workshop was predominantly the demonstration of end-to-end business process flow and following is the business story with classification based on user roles (a.k.a personas)
Business Story:

Picture#4: Business story illustrated with persona/ user role classification
The business story starts with Sales Representative creating a sales order,

Picture#5: Sales Order creation
Details on Sold-to-Party, Ship-to-Party is entered followed by Customer reference and Customer reference date. On selection of material and entering the quantity details, the system understands the material selected is a configured material and Advance Variant Configuration screen is displayed

Picture#5: Advance Variant Configuration screen
In the AVC screen, the initial landing would show that the configuration status is ‘Incomplete’ as the configuration details of the material is not filled.

Picture#6: Variant Configuration determining the price after providing the required attributes
On filling out the required details as per the values the Net value of the material gets displayed. The net value gets changed whenever any attributes are changed. For Eg: Inclusion of SLA agreement
Variant Matching: We can also click on button to evaluate incase there are alternate configurable materials available for the same parameters. On clicking Done, RACR( Review Availability Check Result ) is displayed

Picture#7: RACR screen displaying the confirmed date, plant and quantity confirmation
On return to sales order, costing of the component can be determined by navigating to ‘Extras‘ in menu. The details of the total costs, fixed costs, variable costs and breakup of the component cost is depicted in the below table facet

Picture#8: Costing information of the subassemblies are showcased
On click on Save, Sales Order is created and with this point activity of Sales Executive is complete
Proceeding with the scenario flow, the next business role that performs the activity is Production Planner by executing MRP run for specific plant

Picture#9: MRP run is scheduled with above parameter values
Production Planner checks for the log for successful run of the job scheduled. Next steps is to evaluate stock and requirement situation.
Stock availability can be evaluated by running app Monitor Material Coverage. Select the components that needs to be managed and click on the Manage Material button

On clicking on the Manage Material, cross app navigation is initiated and the user can see the Manage Material Coverage object page with details of the dependent requirements, purchase requisition and planned orders.
Manage Material Coverage app

Picture#10: Manage material coverage depicting shortage of components
Product Planner can simulate depiction of material shortage and accept the proposal by pressing on apply button

Picture#11: Graphical view – depicting shortage of component and its replenishment
Next steps is with Purchaser receiving external procured sub assemblies. App Process Purchase Requisitions. In the list report, scroll to the material components for which Purchase Order needs to be generated

Picture#12: Purchase Requisition to Purchase Order via app Process Purchase Requisitions

Picture#13: Purchase Order generated for Sales Order
On clicking on confirmation section, the column with name Inbound delivery, the user is taken to cross app – Inbound delivery.

Picture#14: Purchase Order app in confirmations section for inbound delivery#
At the menu, user can opt for serial numbers by clicking on Extras


Picture#15: Inbound delivery in confirmations section for inbound delivery#
on clicking on create serial number.., automatically a new number gets generated. Select the sub-assemblies and click on Post Goods Receipt

Picture#16: Post Good Receipt
In the next step inhouse planned orders are converted to production orders using Manage Material Coverage app

Picture#16: Converting Planned Orders to Production Orders
As the Purchase Order and Production Orders are ready, the materials can be staged now for production. To initiate this process launch Stage Materials for Production app

Replenish the Net requirement and stage the materials for production process

Picture#17: Material staging using Production Orders
On staging the production order, now the production order can be confirmed

Picture#18: Confirm Production Operations
Components and Activities like setup time, machine and labor time can be verified at this stage and the material can be posted and set to complete. Goods can be now got to the warehouse by Goods receipt

Picture#18: Goods Receipt for Production Order
The next business process steps is Quality Inspection, here the Quality Engineer inspects the lot of finished goods to approve stocks to be transferred for unrestricted stock
=========
Subsequent sessions focused to explain the end-to-end scenarios of Lot Size of One with classification on user personas as depicted in Picture#1
The business process flow starts from Internal Sales Representative creating a Sales Order in S/4HANA system for Configured Material using Advanced Variant Configuration, the process enables the user to notice costing for the selected material.
The flow proceeds to Production Planner for evaluation of current stock via MRP Run execution at Plant level. Purchasing Specialist on results of inhouse stock.., as per the shortage of material to satisfy the demand, procurement of components is shown resulting in inbound delivery of procured goods.
Production Planner now on receiving the procured components plans for staging of materials and initiates production process. On completion of finished goods, material is moved to warehouse for Quality inspection
Quality Engineers now inspect the finished material and as per the inspection result approves the stock to move it to unrestricted stock or incase of issues during inspection the materials are moved to blocked stock.
Shopping specialist now creates picking, packing and goods issue for outbound delivery / Goods issue from the unrestricted stock is initiated.
The accountant from the finance team now creates billing document, supplier invoice and posts request for payment. Closing the complete cycle of Make-to-order scenario

Picture#5: Business Process flow for Lot Size of One (MTO flow)
Scope Item 55E, covers the span over the following business process flow, involving the different personas / business roles.
Picture#1: Depiction of Business flow with respective personas
Recommend
About Joyk
Aggregate valuable and interesting links.
Joyk means Joy of geeK