

You Wouldn’t 3D Print A House, Would You?
source link: https://hackaday.com/2022/07/13/you-wouldnt-3d-print-a-house-would-you/
Go to the source link to view the article. You can view the picture content, updated content and better typesetting reading experience. If the link is broken, please click the button below to view the snapshot at that time.
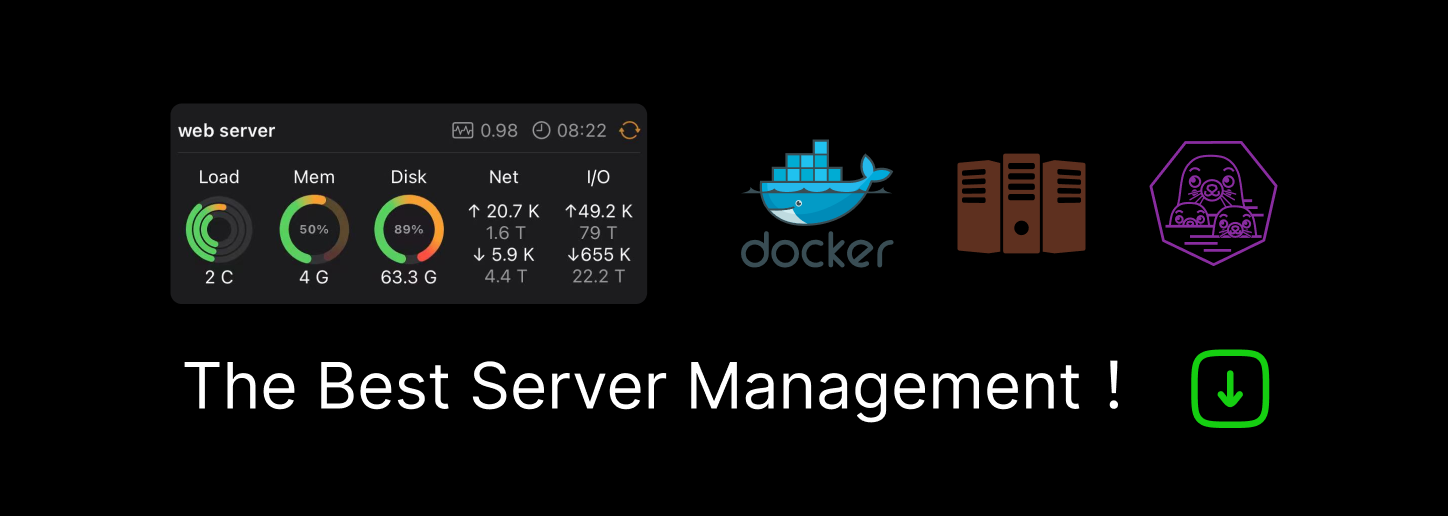
You Wouldn’t 3D Print A House, Would You?
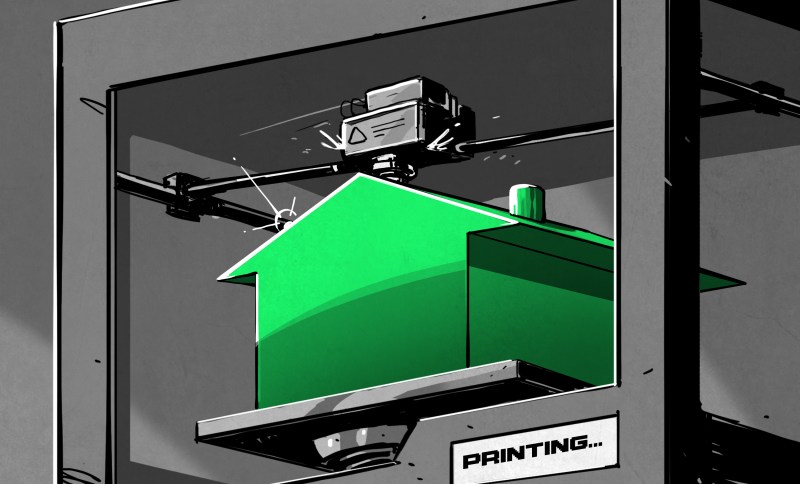
Most houses built in the US today are platform construction: skinny two-by-fours are stacked and layered to create walls with studs. Each floor is framed on top of the other. It is fast, relatively cheap, and easy to learn how to do. However, it is not without drawbacks. Some estimates put the amount of waste generated per square foot (0.09 m2) at around 3.9 lbs (1.8 kg).
Timber framing is an older style where giant beams are used to create the structure of the house. Each timber is hand-carved and shaped, requiring skill and precision. Some cabins are still built this way because it is easy to source the timber locally and cutting into big logs is less work than cutting into lots of small logs. It’s relatively ecologically friendly, but slow and skilled-labor intensive.
We live in a world where there is a vast need for cheaper, faster, more eco-friendly housing, but finding a solution that can tick all the boxes is fiendishly difficult. Can 3D-printed housing accomplish all three of those goals? We’re not there yet, but we’re working on it.
Current State Of The Art In 3D Houses
The idea of a machine to build homes has existed all the way back to 1930. The thought behind 3D-printed houses is that by eliminating some of the human work required, it can scale better and lower costs. But despite the novel machinery, the overall methods of house-building haven’t changed that much. Broadly there seem to be three categories in the market today: prefab, print-in-place, and cut-on-site.
Prefab
Prefab is exactly what you think. Pieces are printed in some facility, ideally close to the building site, and then shipped to be assembled by a team of workers. This allows the prints to benefit from a controlled environment with calibrated and reliable tooling. Or even to print very large pieces like this absolutely massive printer in China. Companies such as Mighty Buildings are working towards prefab modules and whole units that are built from glass fiber reinforced thermoset resin. The benefit of a thermoset material is that it cures stronger and harder than traditional resins you might see in a printer. However, layer-to-layer adhesion suffers as a result.
Mighty Buildings came up with a clever workaround by using multiple UV sources. Layers only partially cure when depositing the top layer and then are cured fully later as the layers stack up above. It is important to note that these buildings are not significantly cheaper or faster than a prefab houses made with traditional methods, but there should be less waste and more flexibility in design.
Print in Place
Print in place often involves a giant 3d printer setup on the site like this one back in 2015. Over the years, advancements have been made making the printer faster, more precise, easier to set up, easier to transport, and so on. However, one area that seems to be much harder to figure out is what to actually extrude.
The real advantage of these systems is they can run around the clock, slowly printing the structures as needed. But if it is printing unsupervised and the nozzle clogs or the layers don’t adhere, it is a big deal. Those who own 3D printers can you imagine starting a four-day print on your printer? One that you can’t just scrape up off the bed and pitch in the recycling when it goes sideways? You need to get it right the first time.
Most companies use some sort of concrete mixture that’s been optimized to flow cleanly through a nozzle. However, concrete isn’t particularly well known for its eco-friendliness as it is a major contributor to greenhouse gases emitted globally.
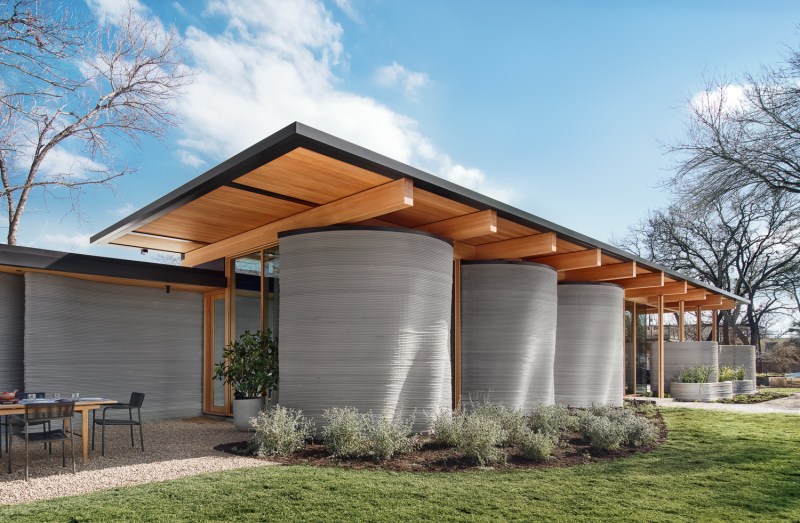
House Zero courtesy of ICON and Casey Dunn
ICON uses a print-in-place method and has produced several houses and is on track to build several hundred more. What’s unique about one of their houses, House ZERO pictured above, is that it leans into what 3D-printed houses are good at. Walls can be any shape: unlike most houses that are square and boxy out of necessity, this house has a sort of wave to it. Whether you visually like it or not, achieving the same effect in the structural elements of the house would be incredibly difficult and wasteful. What is more important is that this house is for sale and is livable.
Cut On-Site
Cut-on-site is a bit of a different approach. It is somewhat of a hybrid between prefab and print in place. It’s not really printed but brings in some of the same ideas. A company brings the machine that creates pieces onto the site but rather than creating one monolithic print, you create smaller pieces that can be built and assembled together as they come out of the machine. A large CNC shipped to the site accepts sheets of plywood and turns them into boxes with holes for insulation, wiring, plumbing, and all the other strange tubes we have running through our walls. Facit Homes is a company that produces homes using this technique. Their CNC router produces “cassettes” according to the design of the house and they’re assembled. While it generates more waste than pure additive manufacturing, each cassette is made from a standard piece of plywood and it makes it easy to reuse and recycle. They’ve produced a dozen houses that are quite modern but otherwise normal-looking homes.
The Verdict
Currently, 3D printed houses don’t achieve their goals of being cheaper, faster, or environmentally friendly. None of the homes we reviewed here were cheaper than traditional methods, and some cost significantly more. While some were faster, there is still the issue of finishing. After the structure of the house has been constructed, professionals need to come and install windows, doors, trim, and all the things we enjoy about homes. Electrical and plumbing also need to be installed in the structure.
Despite their shortcomings, 3D homes have two major strengths. They can create shapes and forms that traditional construction cannot, as seen in the House ZERO. Additionally, they are far less wasteful than traditional construction. Platform construction creates literal tons of waste and 3D-printed structures are printed with only what they need. It’s just in the nature of comparing additive and subtractive manufacturing.
Obviously, this isn’t a complete overview of the industry. There are companies and techniques under development that aren’t covered here. We’s say there’s been slow but exciting progress in the industry. What was a pipedream twenty years ago is now in its infancy — homes have been built and people have bought them and moved in, which is a major milestone. We’ll keep our eyes on it.
Anything we missed? Let us know in the comments.
Recommend
About Joyk
Aggregate valuable and interesting links.
Joyk means Joy of geeK