

CTC扎堆量产,哪家技术最极致?
source link: https://www.eefocus.com/automobile-electronics/519277
Go to the source link to view the article. You can view the picture content, updated content and better typesetting reading experience. If the link is broken, please click the button below to view the snapshot at that time.
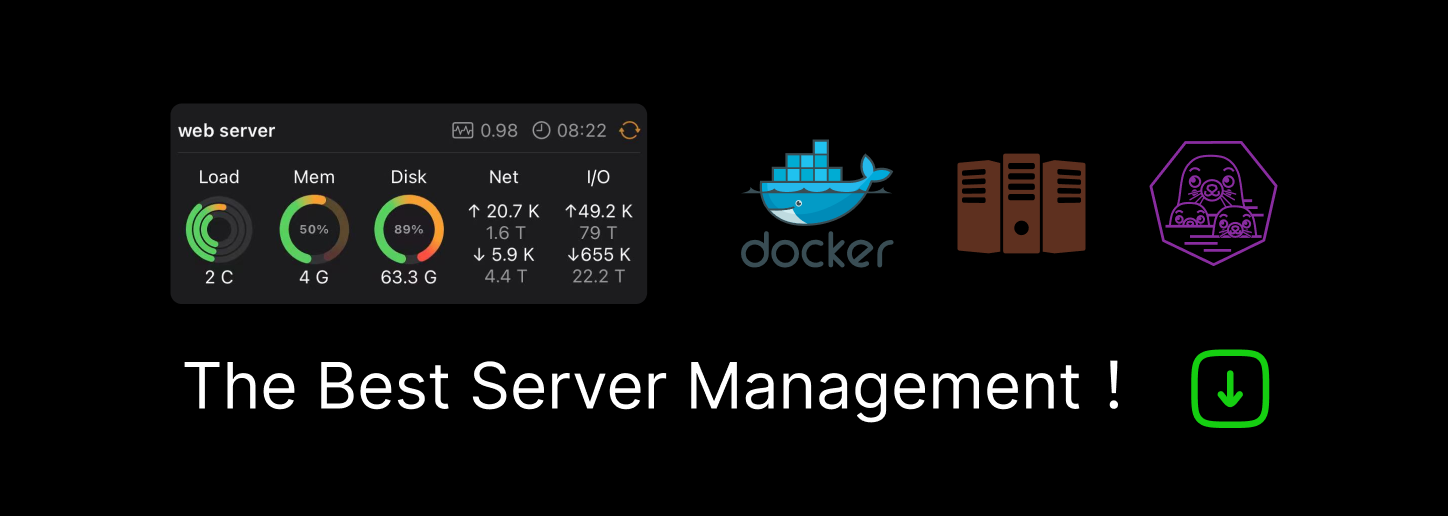
CTC扎堆量产,哪家技术最极致?-汽车电子-与非网
“新技术不应是壁垒,而是带动产业向上突破的阶梯。”
一场疫情,还在不断向中国车市贩卖焦虑情绪。但作为旁观者,更想用“泥泞过后,皆是坦途”来提振信心。由此望向积极的一面,当下电动化转型的浪潮,没有因为诸多不可抗力的出现有所削弱。整个大盘的声量与增势,依旧维持在高点之上。
身处这条全新赛道,纵观那些真正准备充分的强者而言,并未等来想象中的怨天尤人、哀声载道,反而都能根据行业环境的骤变,迅速调整自身节奏,继续展现出手中握有的最强成果。
也正是基于上述背景,本篇文章更想展开聊聊一项近来饱受外界关注的动力电池技术。因为它的落地,智能电动车多方面的性能,再次出现巨大的进步。最终,得以成功普惠终端消费者。
看到这里,相信已经有不少读者猜出,今天的“主角”正是——CTC电池底盘一体化技术。正在进行中的2022,随着类似零跑、特斯拉、比亚迪等越来越多的车企入局其中,并接连拿出手中握有的底牌,大有一副“CTC量产元年”的意味。
那么,仅以目前掌握的信息,不禁好奇谁又将成为其中的“佼佼者”?
结构优化,才是最终解
“动力电池,如同电动车的心脏。”
本段开篇,之所以抛出这样的观点,还是想要证明截至目前,前者对于后者仍具有十分重要的不可替代性。仔细观察不难发现,长久以来动力电池体系的创新,主要还是体现在电池材料与系统结构两个维度。
只不过,随着电池材料部分,尤其是能量密度的提升与进步逐渐趋缓,对于结构系统的创新,已然成为所有人追求的新方向。
换言之,当下影响电动车普及的最大阻碍,无外乎还是续航与成本。可由于锂电池能量密度的原因,其本身所能够提供的续航,已经接近目前理论上的“天花板”,所以很早期大家已经意识到这个问题,转而开始在生产制造工艺与相关结构上,寻求新的突破点。
目前大多数品牌为了“求稳”,依然选择采用——CTM传统电池集成方案,即“Cell to Module”。它的特点是先将电芯组成模具,然后再将数个模组集成为电池包,从下部与车身拼接在一起。
不可否认,站在技术储备稍弱的主机厂角度,CTM仍是其能够掌握最成熟的动力电池安装解决方案,但它的缺陷与短板也是显而易见的。综合而言,模组壳体与车身之间存在着一定的空隙,这也导致车身空间利用率较低,同时整车质量过高。
为此,经过一段时间的研发,CTP无模组电池集成方案,即“Cell to Pack”应运而生。相比CTM,它最大的特点就是跳过模组环节,直接将电芯集成在电池包上,变得更加简单。从而进一步提升了体积利用率、生产效率、能量密度都有所提升,零部件数量也有所减少。
不过,就像特斯拉CEO马斯克曾公开表示的一样,“没必要往盒子里再装一个盒子。”随后,他还举例说明:“原本飞机会把燃料箱放置在机翼之中,但为了更大程度利用空间,便拿掉燃料箱,直接用机翼来储存燃料,这样能容纳的燃料无疑更多。”
话语背后能够听出的含义,直指CTP依然只是过渡方案,并不是动力电池结构优化的最终解。也正因如此,文章开篇所提及,更为极致的CTC电池底盘一体化方案,即“Cell to Chassis”正式走向台前,并开始进入到落地阶段。
同时,相比CTP,CTC是动力电池系统更深层次拓展,直接将电池整合到底盘框架中,进而在结构上实现更高程度的集成化,并且还可以更大限度的优化电池包的重量与空间。
另外,也是非常重要的一点,CTC要求主机厂从更早的阶段,介入车型整体设计之中,这就要求其具备极强的自主研发设计能力。和CTP定义权更多掌握在动力电池供应商手中不同,这一次“主导权”已然交给了前者。
所以明知CTC将成为接下来电动车发展的绝对核心技术之一,但碍于“高门槛”的存在,并不是谁都能立马切入的赛道。
有些优势,与出身无关
实际上,就最近获得的信息,截至目前全球能够真正意义上掌握CTC并成功搭载到量产车型上的品牌,只有三家:零跑、特斯拉、比亚迪。而接下来,更想展开聊聊它们在相关技术路径上的不同与差异。
首先,将目光聚焦于比亚迪。大约一周以前,其正式发布了最新的CTB电池车身一体化技术,即“Cell to Body”。在名称上,与CTC略有不同。
而从结构设计来看,CTB则是把车身地板面板与电池包上壳体合二为一,集成于电池,电池上盖与门槛及前后横梁形成的平整密封面,通过密封胶密封乘员舱,底部通过安装点与车身组装。
更简单来说,即设计制造电池包的时候,把电池系统作为一个整体与车身集成,在满足电池本身的密封及防水要求的前提下,将独立电池包与成员舱再进行密封。
平心而论,采用这样的装配方式,更像是以CTP为基础的一种拓展,让电池包上盖充当车辆地板,或者可以定义为PTC,即“Pack to Chassis”。相比真正意义上的CTC,还是有所距离。
反观特斯拉,早在2020年9月举行的电池日上,就已发布属于它的CTC技术,和比亚迪CTB有着趋同之处的是,其同样满足了电池系统的密封需求,整个电池包的生产制造过程与非CTC电池包类似。
而差异点则为,特斯拉CTC独立电池包的上盖,除了扮演车辆地板的角色外,还将座椅横梁集成于此,最后再与车身整体进行装配。
不过对于上述两家车企而言,因为都需要先制造一个完整的独立电池包,所以不可避免对应的上壳体形状会受到一定限制,进而影响到车身结构效率。最终,导致虽然车内垂直空间有提升,但电池包上部要做加强或缓冲设计,理论上其他边界条件不变情况下,电池内部布置空间和能量密度都会有所降低。
也正因如此,为了规避诸多“痛点”,零跑采取了一条与二者完全不同的技术路径。
按照其官方的描述,“我们通过重新设计电池承载托盘,使整个下车体底盘结构与电池托盘结构耦合,创新了安装工艺。利用车身纵梁、横梁形成完整的密封结构,将电池托盘骨架结构和车身骨架结构合二为一。”
更为通俗来讲,相较于比亚迪、特斯拉,零跑CTC重点是无电池包化,用底盘结构作为电池包外部结构,一体化设计大大提升了结构效率。
此举所带来的好处,也是显而易见的。除了大幅度提升制造环节的效率以及降低对应生产成本外,就拿首款搭载零跑CTC的新车C01为例。
空间方面,通过取消电池上部结构,减少冗余的结构设计,整车垂直空间增加10mm,电池布置空间增加14.5%。
续航方面,具备更好的气密性,可以提升电池保温性能、电池可布置空间等。同时,在AI BMS大数据电池管理系统的加持下,综合提升整车续航里程10%。
性能方面,整车扭转刚度提升25%,轻量化系数达到2.4,提升20%。车身扭转刚度越高,抵御共振能力就越强,意味着整车能够拥有更好的驾控性能,更快的底盘响应效率,NVH性能也能就此提升。
毫无疑问,数字不会说谎。由此站在一个更为宏观的角度,就技术创新性而言,零跑CTC的本质为实现无电池包化,这也是其与比亚迪CTB、特斯拉CTC的最大区别。并愈发彻底的深耕整车一体化架构概念,对于其它新能源车企,也具有十足的借鉴意义。
就方案集成度与落地难度而言,零跑CTC对车身纵梁、横梁均有改动,地板与电池包上盖进行了集成设计,并且电池下托盘也配合车身纵梁一起优化,最终形成了独特的双骨架环形梁式结构。得益于此,不仅整车刚度有了明显提升,同时也解决了密封性的难题。
另外,电池系统无上盖工艺与装配密封工艺,相较传统电池包的制造要求均翻倍增加,零跑能够将这些挑战一一攻克,足以证明其相关方面的技术储备足够的深厚。
不过,作为一家成立不到七年的新势力造车,在与特斯拉、比亚迪两个当下新能源赛道中体量最大品牌的独自交锋中,做到不落下风甚至有所超越,还是不可避免引发来自外界的一些质疑。
作为反驳,更想说,“有些优势,与出身无关。”不了解零跑,切勿妄下结论。
全域自研,不是说说而已
“我们的创新一定要基于电动车和燃油车的差异去创新,而不是盲目地去搞创新。”
此刻,如果非要问及为何零跑能够先于特斯拉、比亚迪,成为国内首家将CTC真正意义上落地的车企,长期以来对于“全域自研”的坚守,必然成为了背后的最根本的原因。而在公司创始人、董事长、CEO朱江明看来,本段开篇的一句话,已然成为他内心深处最为坚守的东西。
当然,数字不会说谎。根据零跑官方公布的资料显示,截至今年5月20日,已获得及申报在途专利1581项;已授权专利1044项;发明专利占总比超过40%。
而这些成就,一跃让其成为专利技术领域覆盖面最广的新势力造车。也正因如此,早在零跑CTC发布会上,按照朱江明的描述,迸发出“电池底盘一体化”灵感的关键,还是由于2016年时,亲眼见证手机由可拆卸电池的功能手机,到集成式电池的智能手机的过程。
彼时,受到启发,旗下拥有强大自研能力的动力电池团队,就已迅速着手攻克相关技术。最终,经过不懈努力,六年后得以成功推出,并一跃占据先发优势。
更加弥足珍贵的是,此刻中国汽车工业借助电动化转型的浪潮,“弯道超车”合资品牌已然成为不争的事实。恰恰基于这样的背景,朱江明清楚的知晓,“新技术不应是壁垒,而是带动产业向上突破的阶梯;一个人可以走得很快,一群人才能走得更远。”
所以零跑CTC揭开神秘面纱后,他也顺势宣布,将会对所有意向车企免费开放,让全球消费者共享科技进步红利,为自主品牌汹汹燃烧的新能源火焰,再添一把燃料。
而将视线重新聚焦于零跑自身,作为首款搭载CTC的新车C01,横向对比同级别竞品特斯拉Model 3、小鹏P7、比亚迪汉包括刚刚开启预售搭载比亚迪CTB的海豹,参数配置上拥有十足的竞争力,加之极具诚意的价格,持续上涨的订单量已然能够证明终端用户的认可。
文末,依然想要强调,无论零跑CTC也好,比亚迪CTB、特斯拉CTC也罢,更多还是想用“各有千秋”所形容,并不是非要横向对比出孰优孰劣。
作为读者,必须明白一点,不同的技术应用在不同车型上,得到的优化参数都是不一致的,主机厂在整车开发中对各方面的考量与权重也都不一样。
所以身处“CTC量产元年”,对于其中的每一位参与者,都应该给予鲜花与掌声,恰恰因为有了它们的存在,智能电动车的赛道才能变得更加宽广与具有竞争力。
而零跑则是其中一个异常努力,最终得以突围的“佼佼者”。
作者丨崔力文
责编丨杜余鑫
编辑丨朱锦斌
Recommend
About Joyk
Aggregate valuable and interesting links.
Joyk means Joy of geeK