

Building a Go-Kart Robot from Scratch
source link: https://spieswl.github.io/projects/2018/building-a-robot-from-scratch
Go to the source link to view the article. You can view the picture content, updated content and better typesetting reading experience. If the link is broken, please click the button below to view the snapshot at that time.
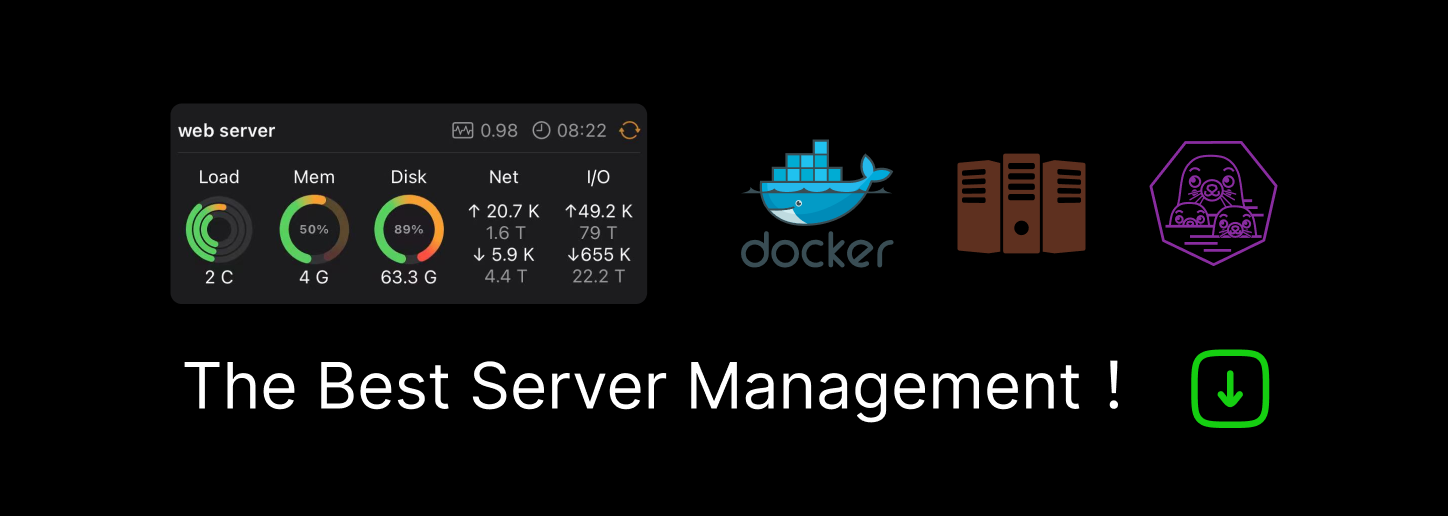
Building a Go-Kart Robot from Scratch
During my time in Northwestern’s MSR program, I took a series of Mechatronics courses that covered several different aspects of robot design. The capstone of the series was a design project to build a shoebox-sized robotic go-kart from scratch and program it to drive autonomously around a custom race track. My go-kart (affectionately nicknamed Cotton Candy after its color scheme) was designed and built over several weeks worth of time in early 2018. Every aspect of the go-kart creation, including mechanical design, electrical controls (with one exception that was provided by the class administrator), the software running on the microcontroller and an attached Android phone, and vehicle assembly, was ultimately my responsibility during the lead-up to the final demonstration. It was a great way to accrue a bunch of cross-disciplinary design experience, and the ‘race’ at the end was exciting for the chance to see all of the other designs and talk shop about the process.
Nick Marchuk, administrator of the NU Mechatronics classes, started our series by kicking us off with workshops that focused on a range of topics in robotic systems design, such as designing controls electronics for motor control, digital signal processing for sensor noise compensation, sensor fusion, mechanical CAD design, and other topics. He also provided us with a small motor control daughter board, designed to work with our self-designed microcontroller PCBs. Lastly, we each created an OnShape profile, as we would be performing our mechanical design through their online CAD system.
With the stage set, the rest of this project write-up just goes through all the discipline-specific areas and talks about my experiences with each. First, look over at GitHub for the project repository which holds the mechanical designs, electrical schematics, and the microcontroller and Android application source code. MPLAB IDE and Android Studio were used for emdedded device programming, and Autodesk EAGLE was used for the electrical schematics and PCB layout.
The vehicle itself is a differential-drive system, with the wheels driven by two Chihai CHR-16G-050-ABHL 12V, 3.3W DC motors and controlled with a PIC32MX250F128B microcontroller. The Android phone on top (on my vehicle, this phone is a OnePlus One running Android Marshmallow) is needed for its rear-facing camera. The nominal design uses the phone’s rear-facing camera to perform line detection via a custom Android application that was sideloaded onto the phone. The rear-most caster, 12V lithium-ion battery, wheel collets/caps, and miscellaneous wiring and fasteners were all hand-picked, although in the battery’s case we were given limited options to choose from. All of the mechanical chassis pieces were designed by myself and either 3D-printed (with PLA) or laser cut (from cast acrylic sheets).
Mechanical Design
The mechanical design of the vehicle was where I got most creative. All mechanical design was done in OnShape, and you can click on the preview images below to inspect the final detail drawings (which are included in the GitHub repo).
The wheels are a vibrant shade of pink as our 3D printer in the MSR lab only had pink filament available. As it turns out, the use of color gave the finished product a nice look (though I wish I had picked out blue wheel hubs, instead of the red hubs). The twin wheel channels for O-rings was a particularly savvy idea, as it allowed for more grip and ground contact when compared to some of the thinner wheel designs that only had room for a single O-ring. The trade-off was a longer 3D print time, but the improved performance on inclines was well worth the extra time spent on the print bed.
The chassis (both the mounting surface and the front phone support bracket) was cut from a single blue sheet of acrylic. Thanks to the Ford Engineering Design Center’s laser cutters, the mounting holes and other cutout details were a breeze to handle. Nearly everything was secured with assorted bolts, washers, and nuts, although the motor power/encoder cables were secured with tie-wraps to keep those from moving around when the kart was driving.
The phone support bracket at the front of the vehicle was specifically designed to elevate the top portion of the phone. With a slight upward angle to the phone, the rear-facing camera is able to look slightly ahead of the drive axis.
The battery and motors are clamped to the chassis with custom-fit, 3D-printed pieces. The control electronics are on stand-offs to allow some cable routing underneath, and also to provide a secure mounting point to the rest of the body. As a result of all this, excluding the phone, the vehicle has no loose parts.
Electrical Design
The electrical design was oriented around several design constraints, most of which involved the need for peripheral motor control and a USB OTG interface to the Android phone. As mentioned earlier, core processing was handled with a 32-bit PIC32MX250F128B microcontroller. Most components were sourced from either DigiKey or Sparkfun, although there were a ton of components laying around the lab that our classes were also permitted to use. The left two images show the final, populated, soldered control board, before I mounted it to the chassis.
The supplied daughter board, which had a ready-to-go design for PWM motor control, can be seen on the far right. Our responsibilities were simply to populate the board and plug in the peripherals.
Spacing for the 8-pin header interface provided the only position constraint for the PCB design, though I elected to use surface-mount components in order to cut down the amount of vias needed to connect everything. The system design includes the microcontroller, two status LEDs (one power, one user-configurable), the power supply, two pushbuttons (one master reset, one user-configurable), the programming port, the USB Mini port, and the headers for the motor controller board. Schematic and layout were both done with Eagle, and are shown below.
All members of the ME433 class used a third-party PCB manufacturer, PCBWay, to do the board manufacturing. I did the all of the soldering and board testing myself, so I was pretty happy when everything worked like a charm. I also really like the nice, clean look that my PCB ended up with, and the post holes in the corner were exactly what was needed to secure the standoffs, resulting in a sturdy connection to the rest of the chassis.
Software Design
The software design was split into two distinct parts:
- The main microcontroller program, and
- The line-finding Android application.
The high-level structure of the software is as follows: The microcontroller code, written in C
, initializes and sets up an internal state machine. It then immediately attempts to open a socket to the Android phone via USB OTG. The microcontroller uses data from the phone application, written in Java
, to determine how to drive the motors via a PI control loop. The system continually runs through the [app<->PI control] sequence until powered down.
The microcontroller uses a single PI controller, looping at a modest (about 50 Hertz) frequency to output two individual PWM signals (one for each motor). The PWM signals are clamped to fall in a range that corresponds to 0-100% motor power. Depending on where the microcontroller “perceives” the line to be, it will raise or lower the left or right motor power appropriately, while attempting to maintain some amount of forward velocity. The PWM frequency itself is set to about 20 kilohertz.
The microcontroller “perceives” the line position by being told where the line is in the camera’s field of view. Thanks to Harmony
, a set of Microchip-provided libraries, the microcontroller can receive data via USB OTG while a phone application is running. The Android application intercepts the camera stream and does color segmentation to identify a specific, colored line on the track-in this case, I am picking out the red portion of the line. The application passes along the line position by passing an integer value that represents the line position in pixel coordinates on the rear-facing camera image plane. Since I know how wide the camera image is, I can set center-image values to correspond to equal power applied in the forward direction for both motors. Everything outside of the center then triggers a scaled change in applied motor power.
There are plenty of other clever things done in the code, such as exposing controls for color saturation and intensity thresholds that can be tuned on the phone’s display, to more easily work around ambient lighting changes.
You can see an example of the course at right. NOTE that there is an inclined ramp cross-over, which isn’t shown on this image file, that connects the vertical straightaway and closes the loop on the track.
As for the competition, my cart traversed the course in just over 2 minutes, which put it into the top quarter of the time trials. The incline cross-over in the middle gave many of the other teams all kinds of trouble, since most of the robots could not generate enough traction to get up the slope, so most of the results ended up being marked down as “Did Not Finish”. I cannot complain about my robot getting relatively good results, yet I am happy with how this robot evolved even if I just look at it from a design perspective. I also think it would be a neat extension to come back and iterate on this robot’s design, if I can find a more practical use-case for such a robot in the future.
Recommend
-
11
Steve Hannah Another true story from my childhood, that I call “The Go-Kart”. Enjoy: I wheeled the Go-k...
-
10
snes-kartBuild fast, full-stack web apps in your browser for free
-
9
Nintendo sold 10.6 million copies of Mario Kart 8 Deluxe last year Did you miss GamesBeat Summit 2021? Watch on-demand here!
-
6
This is the latest in my series of screencasts demonstrating how to use the tidymodels packages, from just starting out to tuning more complex...
-
2
Nintendo's 'Mario Kart Live: Home Circuit' is on sale for $75 right nowThat's a return to a record-low price for both the Mario and Luigi sets.
-
8
Here’s Mario Kart, as played by a neural network Watch and learn By
-
10
Get a Nintendo Switch and Mario Kart 8 Deluxe for only $300Many Switch games are also on saleEven though we’re still a matter of days away from Bla...
-
6
Site ColorhexText ColorAd ColorhexText Color
-
7
Waluigi Pinball next time? Please? — Mario Kart 8 Deluxe’s new expansion is good so far—but is it worth $25? Believe it or not, the best track so far comes from the s...
-
5
Outrace Family Guy, American Dad! and King of the Hill characters in Warped Kart Racers
About Joyk
Aggregate valuable and interesting links.
Joyk means Joy of geeK