

Photonic Wire Bonding Process Could Open Door to More Photonic Electronics
source link: https://www.allaboutcircuits.com/news/photonic-wire-bonding-technology-fabrication-challenges-for-photonic-integrated-circuit-development/
Go to the source link to view the article. You can view the picture content, updated content and better typesetting reading experience. If the link is broken, please click the button below to view the snapshot at that time.
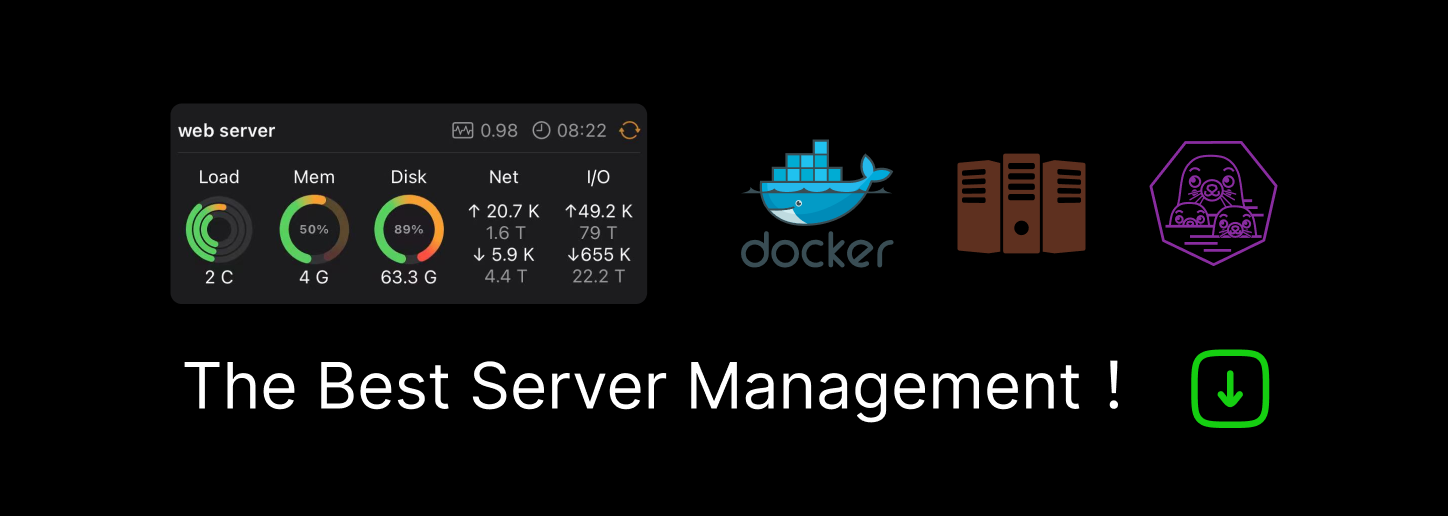
News
Photonic Wire Bonding Process Could Open Door to More Photonic Electronics
As photonics technology seeks its niche in the industry, one hurdle to overcome is a scalable fabrication process. One technique called photonic wire bonding (PWB) hopes to push photonics forward.
Over the last couple of years, researchers have been making tremendous progress in photonic packaging and integration.
Advancement in the technology has led to the fabrication of highly integrated photonic integrated circuits (PIC) while adopting scalable micro- and nano-fabrication techniques geared towards solving the challenges associated with photonic inter-chip connectivity.
An illustration of a silicon PIC. Image used courtesy of Carroll et al
While offering a high bandwidth, low power, and small form factors, PICs finds applications in a wide range of sectors, including telecommunications, data centers, RF systems, etc.
Despite the push for creating more photonic technology, there are a few challenges facing this technology, especially when it comes to fabrication.
With that in mind, this article will go over one major challenge, photonic wire bonding, and how it plays into PIC development.
Overcoming Photonic Wire Bonding Limitations
Traditional photonic devices are usually connected by standard single-mode fibers. Unfortunately, this technique for connectivity can create a mismatch between the optical mode of the strongly-guiding on-chip waveguides and the optical fiber.
What's more, the minimum achievable interconnect density is determined by the fiber's cross-section, which can be relatively larger than the geometrical footprint of the on-chip component.
To surmount these limitations in photonics interconnects, researchers at the Karlsruhe Institute of Technology (KIT) have developed a PWB technique that offers the potential to connect and integrate photonic devices in a bid to realize flexible and high-performance multi-chip systems.
Overall, this technique claims to be a good choice for the industrial production of optical modules.
Using the photonic wire bonding technology, the researchers have, in the past, fabricated a 400 Gbit/s silicon photonic transmitter module which comprises an array of eight laser sources that feed an array of eight silicon photonic Mach-Zehnder modulators (MZM).
The development of this technique has helped to spur photonics research and device creation. Hoping to leverage this PWB technique, a collaboration aims to integrate it on a larger scale.
Collab Open More Doors for Scalable PICs
PWB technology generally targets the growing demands of low-loss optical interconnects in state-of-the-art photonic sub-assemblies.
Hoping to leverage PWB techniques to facilitate the fabrication of next-gen highly integrated photonic devices, Freedom Photonics is leveraging Vanguard Automation's SONATA and REPRISE 1000 systems.
The two devices use 3D nano-print technology to fabricate waveguide optical interconnects between two components (PWBs) or facet attached micro-lenses (FAML) to couple light using a 2-photon lithography process.
While the SONATA is a lithography unit that performs structural operations of PWBs and FAMLs, the REPRISE is responsible for all the pre- and post-processing steps, including dispensing, removal of an unexposed resin, cleansing, and encapsulation of the bonds.
How is a Photonic Wire Bond Made?
Manufacturers follow a step-by-step process to fabricate photonic wire bonds. Moreover, the fabrication process employs three-dimensional direct laser writing (3D DLW) based on multi-photon induced polymerization.
The photonic materials are first mounted on a planar microscope cover glass or a metallic sub-mount. This sub-mount performs mechanical ground plate, a heat sink, and electrical contact functions.
Then, bare dies are placed on the sub-mount using polymer adhesives, conductive adhesives, or soldering technologies.
A typical example of a photonic wire bonding process. Image used courtesy of Lindenmann et al
Furthermore, the sub-mount and photonic components are cleaned by successive rinsing with ultra-clean acetone and isopropyl alcohol to remove organic remains and loose inorganic particles.
After sample preparation, the optical module and a resist material are inserted into a 3D direct laser writing lithography system. In addition, a photoresist material is deposited between the interconnect regions of the feed waveguides.
A combination of a camera and computer vision techniques for pattern recognition is used to obtain a visual impression of the optical feed-waveguide. At the same time, the shapes of the PWBs are adapted to the actual positions of the integrated waveguide facets.
Based on the measured coordinates of the waveguide outlets, the structure of the emerging photonic wire bonds is calculated. However, the calculated structure is transferred into single writing lines consisting of single points consecutively addressed by the lithography system to generate a machine-readable dataset.
Finally, the non-polymerized resist material is removed in a developer bath. During the fabrication process, no high-precision active alignment is needed since the waveguide geometry is adapted to the relative positions of the photonic subsystems.
Next Steps for Photonic Wire Bonding Fabrication
The photonic wire bonding technology developed by the researchers at the Karlsruhe Institute of Technology is focused on chip-to-chip photonic connections. A further stride would be to incorporate PWB interfaces between on-chip waveguides and single-mode fibers.
In addition, the assessment of different resist materials that can be structured by two-photon polymerization is also important to investigate.
A close-up view of a photonic wire bond interconnects. A typical example of a photonic wire bonding process. Image used courtesy of Lindenmann et al
All in all, the photonic wire bonding technology is keen to offer photonic systems with high packaging density and increased design flexibility of photonic integrated circuits.
Interested in other photonics news? Read on in the articles down below.
Integrated Photonics May Solve Power and Speed Issues of Massive Data
Researchers Leverage Photonics in Radar System to Detect Down to the Millimeter
Intel’s Integrated Photonics Research Lab Could Help Propel Photonics Mainstream
Recommend
About Joyk
Aggregate valuable and interesting links.
Joyk means Joy of geeK