

The supply chain data gap must be closed - Oracle explains why its new logistics...
source link: https://diginomica.com/supply-chain-data-gap-must-be-closed-oracle-explains-why-their-new-logistics-functionality-will
Go to the source link to view the article. You can view the picture content, updated content and better typesetting reading experience. If the link is broken, please click the button below to view the snapshot at that time.
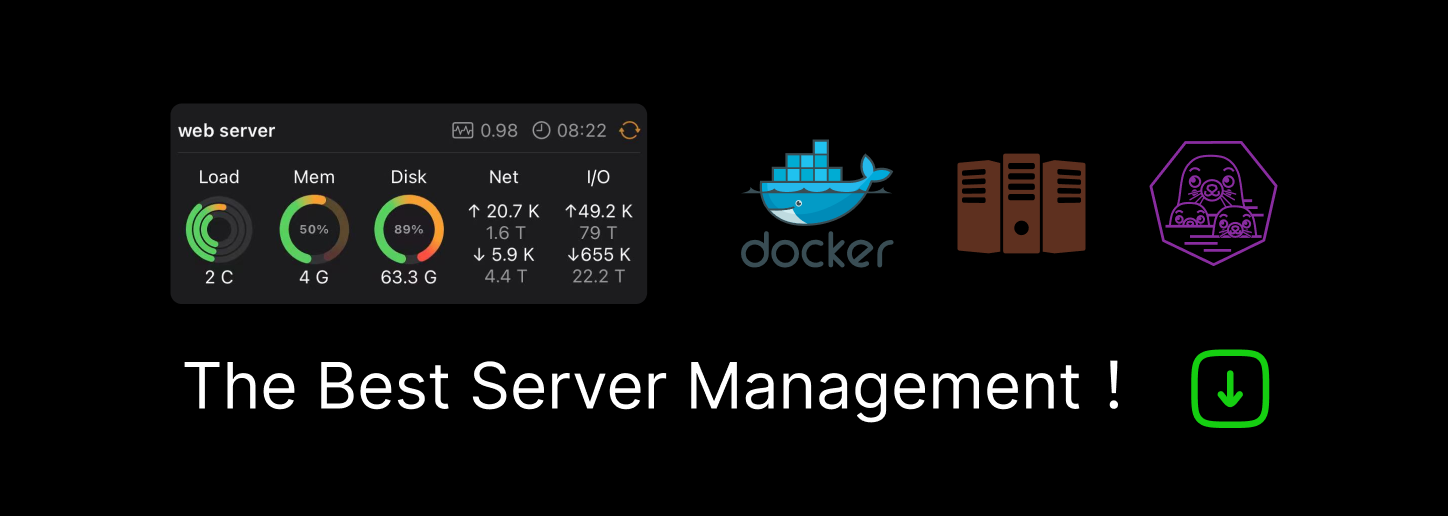
The supply chain data gap must be closed - Oracle explains why its new logistics functionality will ease customers' supply chain challenges
Truth: I make fun of writers who craft articles based solely on press releases. But, I did it myself - twice. In my defense, it was in 1992. I was pushing to write an entire edition of a new arts and entertainment weekly. Even then, I knew that the article was fluffy flaff. I vowed I would always go beyond the press release.
Oracle just issued a press release, Oracle Introduces New Logistics Capabilities to Help Customers Increase Supply Chain Efficiency and Value. To be fair, Oracle's press releases are on the substantive side, as far as those things go.
Oracle has been great about getting on video and hashing out the trends behind the news. This time, we didn't have a chance to do that, but worry not, I was able to dig in via email. My agenda? As always: what customer realities does this news respond to?
An above-average press release starts with a problem statement. The problem here is painful, if obvious:
- A recent Oracle survey found that 87 percent of people have been negatively impacted by supply chain issues over the past year.
Oracle survey - 91 percent of consumers consider the supply chain when making a purchase
No surprises, but Oracle's survey of 1,000 US consumers certainly validated the problem. The survey was released in September 2021, when we were in the throes of the Delta variant, but I have no doubt we'd get similar numbers today:
- Almost half (45 percent) of people admit they never thought about how products were delivered prior to the COVID-19 pandemic, but now nearly everybody (91 percent) considers the supply chain when making a purchase.
Here's the most notable part for enterprises: the data on purchasing behavior changes. If brands don't adapt, they'll lose customers to brands that do. More from the supply chain survey:
- 91 percent of people plan to change their buying behavior moving forward, including buying in bulk and stocking up on items (49 percent), purchasing gifts earlier to allow for delays (45 percent), and paying closer attention to global shortages of items they regularly use (40 percent).
- 81 percent of people are willing to pay a premium for smooth and timely delivery of their items.
- 84 percent say delays would cause them to cancel their order, and 80 percent say delays or shortages would even cause them to stop buying from a brand entirely.
I was particularly struck by this data point:
- People want brands to provide more regular updates about shipping status (63 percent), be more transparent on inventory (59 percent) and potential supply chain issues (54 percent), and offer refunds (56 percent) or discounts (52 percent) if items are delayed or cancelled.
Supply chains (and transportation systems) lack product visibility
The lack of transparency, visibility, and communication about supply chain issues is often worse than the delays themselves. Tell me how long the product is delayed, and where it is. Make it possible for me to adapt - and earn my trust. Alas, I've found even the supposed global logistics leaders, Amazon and Walmart, are profoundly unable to pinpoint products in transit, and update accurately on delays.
Therefore, Oracle concludes:
The unpredictability of the past two years has created major logistics-related challenges for organizations, as they navigate large fluctuations in supply and demand and major disruptions to their distribution networks.
Thus, the rationale for the latest supply chain features:
To help organizations increase efficiency and value across their global supply chains, Oracle today announced new logistics management capabilities within Oracle Fusion Cloud Supply Chain & Manufacturing (SCM).
Unlike the Oracle of old, today's Oracle is always ready with a customer quote. Cue Joseph Hodges, Director of Logistics Center of Excellence, Western Digital:
Western Digital has multiple manufacturing locations in the US and Asia, handling more than half a million shipments every year. Our supply chain ecosystem is extremely complex with multiple end markets each having unique service needs, and the disruptive events of the past two years added to that complexity on an exponential scale.
With Oracle Transportation Management as our foundation, we have been able to streamline logistics processes and customer support, quickly achieving significant results - including reducing cost and service disruption through expansion of our partner base, implementing on-demand spot bidding, and dynamically shifting modes while operating with 90 percent touch-free automation in the last fiscal year. In addition, Oracle Transportation Management's built-in machine learning capabilities have helped improve ETA accuracy from 64 percent to 93 percent, which is an invaluable result in terms of an improved customer experience.
That last quote on ETA accuracy improvements jumped out. Pinpoint availability; provide customers with a reasonably accurate update. This is not as easy as it sounds - transportation systems are notorious "black boxes" when it comes to pinpointing product location (I suspect most readers have checked a UPS or FedEx tracking update, and seen for themselves how often their package goes dark).
Oracle's supply chain functionality - updates
Which features are Oracle announcing? Here's the summary, lightly edited by me:
- Intelligent Transit Time Predictions -A new machine learning algorithm in Oracle Transportation Management will enable users to evaluate the potential impact of both macro-level interruptions (including extreme weather or airport delays) and network-level disruptions (such as labor and capacity shortages).
- Enhanced Shipment Capabilities - Supply chain leaders can simplify and automate transportation processes for shipments. New capabilities include automated spot bidding and the ability to combine and track multiple shipments in Oracle Transportation Management, and automated global trade analysis on trade agreements in Oracle Global Trade Management.
- Multi-Language Digital Assistant - Real-time, multi-lingual response capabilities within Oracle Logistics Digital Assistant... Enable organizations to provide faster and more accurate information and standardize responses to inquiries in their customers’ native languages.
- Advanced Transportation and Global Trade Analytics - New advanced analytics capabilities enable customers to access, analyze, and interpret highly accurate transportation and global trade data.
Behind the SCM product news - email Q/A
If solving supply chain issues was easy, we wouldn't get survey results like these. So, I fired off some questions inspired by Oracle's SCM news. Derek Gittoes, VP of Supply Chain Management Product Strategy at Oracle, drew the short straw was the lucky one who responded to my questions.
diginomica: Why has transportation (and visibility into transportation systems) been such a sticking point for supply chain management the last couple of years? What does it take to get to a better approach? Better technology? More buy-in from employees to enter data, or can that be automated? Do individual parcels and packages and items need smart tags for tracking, or is that overkill? (Will we eventually have such tags on our luggage?)
Gittoes responded:
The fundamental problem is that freight can't talk. Whereas passengers will make noise immediately if their travel plans are impacted, freight (luggage included) often requires someone to notice there's a problem before any action is taken (and it's often too late to make a difference). The solution to better transportation visibility lies in technology. Transportation visibility (i.e., knowing the current location and condition of a shipment of goods and an estimate of when it will arrive at its destination) has improved tremendously over the years thanks to advances in technology.
Gittoes argues that these tech improvements are well underway:
For example, satellite- and cellular-based tracking technology along with mandated use of Electronic Logging Devices (ELD) has greatly improved visibility for truck-based shipments in the US market. In addition, there have been advances in transportation management software technologies like Oracle Transportation Management that process that shipment visibility data to make smarter decisions (e.g., predictive arrival times to proactively identify shipments that are at risk of being late due to congestion, weather and other factors).
Smart tags and related IoT-based technologies are being used today in some scenarios, and as that technology becomes cheaper and more widely adopted, transportation visibility will continue to approve.
Fair enough, but as I pointed out in the email, better data doesn't always lead to better decisions. That begs the question: how can something like global trade analytics lead to better decision making? is it a matter of getting the right type of data into these analytics systems? Or are there other keys, such as easy-to-consume dashboards, or prescriptive AI recommending best actions, or alerting to potential costly delays or poor trade route conditions, etc.?
Gittoes responded:
Better decisions stem from getting the right information to the right people at the right time. The new analytics capabilities in Oracle Transportation Management and Oracle Global Trade Management enable analytics information to be embedded within the same workbenches that the global trade analysts and transportation planners are using to perform their daily functions.
How does that work in the field?
For example, a global trade analyst can easily see which imported items are incurring the highest import duties and see if those items are eligible for a preferential duty agreement. If the potential savings are high enough, they can then take action by working with the suppliers of those items to collect the necessary documents (e.g., certificates of origin) to qualify the items and take advantage of the preferential duty rate when importing them.
Gittoes cited another example: transit variance, supported by machine learning:
Likewise, transportation analysts can easily see where there is a high variance between planned and actual transit times along with the factors that influence those variances (machine learning is used to determine which factors have the most influence). For example, it may be that shipments that depart on a particular day of the week incur more delays and therefore the planner should try to shift the transportation activity to another day of the week with more reliable service.
My (quick) take
I agree with Gittoes: the tech that will aid supply chain visibility is improving. We are also getting better at surfacing the data that will lead to better analytics (and decisions). However: the combination of higher consumer expectations and global supply chain volatility makes the problem harder - and more pressing. That's exposed the gaps, and there are plenty. Gaps in processes, data, and, as the survey found, consumer expectations.
Obviously, vendors like Oracle are aggressively pushing to close these gaps. The best way to assess each vendor's effectiveness is via validated customer use cases. The numbers cited by Western Digital are encouraging; I look forward to digging into other examples as we talk to Oracle (and its customers) further this year.
Recommend
About Joyk
Aggregate valuable and interesting links.
Joyk means Joy of geeK