

多晶硅的世纪之争
source link: https://www.36kr.com/p/1491090602174336
Go to the source link to view the article. You can view the picture content, updated content and better typesetting reading experience. If the link is broken, please click the button below to view the snapshot at that time.
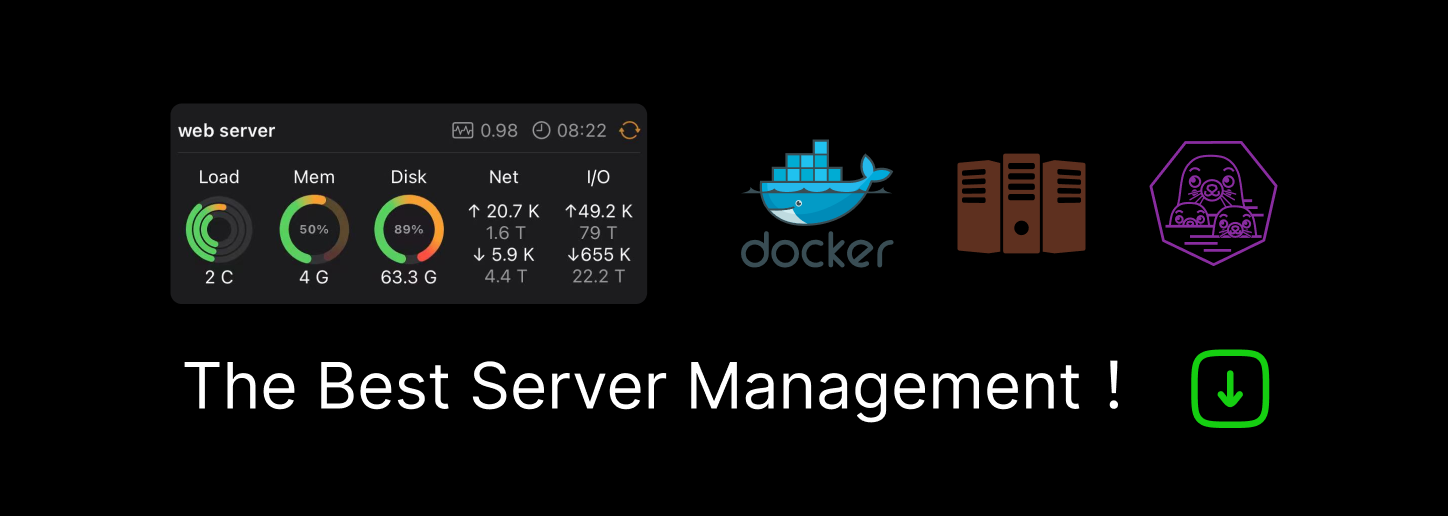
随着光伏装机成本的持续下降,光伏装机量迎来快速增长。由此带来多晶硅再度供不应求,年内涨幅超200%,多晶硅的供需失衡甚至已经影响到了下游的装机量。
国内硅料企业纷纷开启新一轮的扩产大潮。对于多晶硅生产的两大技术路线,市场出现两级分化。改良西门子法还是流化床法,又一次成为争论的焦点。由于多晶硅的重要性,技术路线选择,这次路线之争无不牵动广大新能源投资者的神经。
早在上世纪五六十年代,多晶硅生产的两大技术路线相继问世,其中西门子法通过多次技术迭代一直引领行业前行,成为世界的主流路线,而流化床法作为第二技术路线也在持续进步。
在“双碳目标”的背景下,光伏成为可再生能源的主力,这场跨越世纪之争的答案也越发清晰可见。
01 为什么多晶硅的技术路线如此重要?
【1】多晶硅的行业地位
能源革命的浪潮之下,光伏的重要性目前已再无分歧;从产业链的视角来看,多晶硅作为光伏产业的上游原材料,其在整个光伏产业中占有举足轻重的地位。同时多晶硅也是集成电路最为关键的基础原材料。
图1:光伏产业链示意图,资料来源:新疆大全招股说明书
首先,多晶硅的成本与光伏发电系统的成本直接挂钩。早在2014年,国家发改委能源研究所等研究机构发布的《中国可再生能源发展路线图2050》就提出,2025年光伏要能实现全面平价上网,那成本下降就成了光伏产业进步的不竭动力,而其中的大头就是硅料。发展初期,多晶硅的成本曾一度占太阳电池的近50%。
回溯光伏过去十余年的发展,光伏成本从50元/W下降到了4元/W左右,多晶硅环节的持续降本为光伏平价上网做出了巨大的历史贡献。
图2:产业链各环节价格(元/W、元/kg),资料来源:中国有色金属工业协会硅业分会,国信证券
根据BP发布的2020年能源展望数据,到2050年,光伏发电的成本较2018年还能下降70%。这必然要求光伏产业链各个环节共同努力,多晶硅最为材料源头,将长期担当降本增效的重任。
图3:未来30年光伏成本下降曲线,资料来源:BP Energy
其次,多晶硅的质量的提升促进光伏的技术进步和国产替代。自2018年初开始,单晶硅片产能规模快速扩张,成为行业主流,为满足下游需求,国内多晶硅企业在积极扩张的同时,也加速了光伏级硅料品质的提升。目前通威股份、新疆大全的特级料占比均超过90%。
与此同时,我国多晶硅料品质的提升,对于硅料进口依赖的下降功不可没,根据硅业分会的数据,硅料进口占比已经从2016年的42.1%下降至2020年的20.2%。2021年1月,通威股份已实现N型硅料的批量生产。
时至今日,我国多晶硅产业已取得了长足进步,从产业化早期的几乎完全依靠进口到目前产量已占全球的三分之二,国内的产销规模已经位居全球首位。但在太阳能光伏平价上网的倒逼下,多晶硅降本增量之路还在继续。
第三,终端光伏装机需求带来多晶硅的增长
多晶硅也是一将功臣万骨枯的行业,打的头破血流,最终呈现强者恒强,两极分化的局面。头部企业凭借技术和成本优势维持较高水平的产能利用率。如通威股份,2017-2019 年产能利用率分别为93.70%、96.38%、92.46%,2020年上半年达到了116%。而中小企业产能利用率较低,部分企业由于投产较早、设备陈旧、规模较小,已逐步停产。
据《中国能源报》统计,国内在产高纯晶硅企业数量由2018年初的24家,减少至2019年初的18家,再缩减至2019年底的12家。
图4:2008-2019年中国多晶硅产量及占全球产量的比重,资料来源:中国光伏行业协会,新疆大全招股书
【2】多晶硅的生产是门技术活
跟锂电池行业的上游原材料不同,多晶硅料具有高载能、重资产、扩产周期长、技术壁垒高的多重特点。所以多晶硅看似工业标准品,实际上更多的属性是化工品。正因为此,多晶硅的技术能力是衡量多晶硅企业的硬核能力之一。
按纯度要求及用途不同,可以将多晶硅分为太阳能级多晶硅和电子级多晶硅,太阳能级多晶硅主要用于太阳能电池的生产制造,而电子级多晶硅作为主要的半导体电子材料,广泛应用于电子信息领域。
太阳能级多晶硅对杂质有严格的要求,通常要求其中杂质总含量低于10-6,即多晶硅的纯度需达到99.9999%以上。而电子级多晶硅可以说是技术巅峰,其纯度要求高达99.999999999%(不用数了,小数点后面是9个9),相当于1000吨的电子级多晶硅中总的杂质含量不到一粒花生米重量的1%。所以世界范围内能够生产电子级多晶硅产品的企业屈指可数,电子级多晶硅成为行业高地。
总的来说,高纯多晶硅的生产不是煤炭那种简单粗暴只拼产能的行业,它是光伏产业链中技术含量较高的环节,加上投资大,风险高。目前国内隆基、中环等垂直一体化的企业也没有直接下场,而是采取参股的方式参与到多晶硅生产。
图5:下游企业通过参股方式绑定头部多晶硅企业(万吨),资料来源:各公司公告,国金证券
02 “一大一小”技术路线
【1】改良西门子法
对于光伏业内人士而言,西门子法是再熟悉不过了,这是目前国内外最普遍也是最成熟的方法。根据中国光伏行业协会的数据,2019年全球多晶硅产量中采用改良西门子法生产的占比高达97.8%;我国也类似,2020年国内采用改良西门子法生产的多晶硅约占全国总产量的97.2%。
今天成熟的改良西门子法最早由德国西门子公司在1955年发明,在过去60多年中,业内参与者不停的对西门子法进行技术优化和提升,已经改良到了第三代。其优点已经非常突出。目前全球前十硅料生产企业的技术路线都以改良西门子法为主。
图6:全球前十硅料生产企业,资料来源:国信证券
纵观全球多晶硅的发展历史,基本上是和西门子法技术路线的技术进步同步的。
具体而言,还原炉的材料从石英玻璃发展到金属再到不锈钢,其内部的棒数也逐渐从1对棒、3对棒逐渐提升到48对棒以上的大型还原炉,还原炉产量已从1975年的单炉40吨/年,提升至现在600吨/年的水平。
多晶硅技术的进步已经和规模的扩大形成正向循环,收益规模大型化、技术优化,改良西门子法多晶硅单位产能投资成本大幅下降,多晶硅生产线投资成本从2008年千吨投资成本约为7亿元~10亿元降到现在的1亿元/千吨以下。
根据工业发展规律,未来随着规模产量的继续扩大,改良西门子法的竞争能力将会进一步强化,主流工艺地位进一步稳固。
图7:西门子法生产工艺,资料来源:《当代多晶硅产业发展概论》
【2】流化床法——现实与理想的差距
下面敲重点,讲讲最近备受关注的流化床法,其实长期关注光伏行业的人知道,西门子法的应于一直远大于流化床法。但并不新鲜的流化床法之所以又引起大家的注意源于协鑫,叠加光伏这个黄金赛道,其核心要义就是降低成本,所以每个更降本扯上关系的新技术势必都让市场很亢奋。
在我们长期关注的动力电池领域,也有类似的例子。今年年初,广汽就曾发布“石墨烯电池”表示具备6C快充能力,最快8分钟就能充电至80%,此举引来不少吃瓜群众围观。同样的例子还有特斯拉的4680圆柱电池,这还尚未量产,相关板块已经涨了一轮。
回到流化床法上,最早是美国联碳公司在1952年开发出将硅烷分解沉积在固定床上硅颗粒表面的技术,这也是流化床技术最早的雏形,数年之后,杜邦公司在1961年申请了使用三氯氢硅为原料在流化床内生产颗粒硅的专利,标志着流化床法正式面世。
同样师出名门,但流化床法的工业化之路异常艰辛,难有大为。西门子法经过多次技术迭代已然成为多晶硅企业的主菜,流化床法虽有进步,却难于大规模量产,长期作为配菜。
那么问题来了,流化床法比西门子法晚了6年,但对于60余年的时间跨度,可以说两者是处在同一起跑线。为什么流化床法此前一直备受冷落?
图8:流化床法制备多晶硅技术的发展历程,资料来源:《当代多晶硅产业发展概论》,国金证券
1) 基本原理
流化床法的主要原理是将硅烷用氢气作为载体,像气流一样从流化床反应器底部注入,然后上升到中间加热区反应,因为有底部进料时候的气流源源不断的进入,可以让反应器内的籽晶沸腾起来,处于悬浮状态,注入的硅烷等原料和氢气在加热区发生反应,然后,随着反应的进行,硅逐渐沉积在悬浮状态的硅籽晶上,籽晶颗粒不断地生长,长大到足够重量的时候,硅颗粒沉降到反应器的底部,排出的就是颗粒硅。
图9:改良西门子法与流化床法核心设备对比,资料来源:《当代多晶硅产业发展概论》
2) 令人着迷的优势
相对改良西门子法,流化床法的最大优势主要体现在流化床反应器上。
其一,由于底部进料的气流存在,硅籽晶处在悬浮状态,可提供更大的反应面积,从而获得较高的反应效率,硅颗粒生长速度更快;同时,流化床反应器内是体和固体接触好,热能传递效率高,电耗自然就降下来了。能耗相对较低。在于参加反应的颗粒硅晶种表面积大,沉积速度(生长速度)大幅提高,故生产效率高,大大减少了能源消耗,降低了成本。
其二,从上图中可以看到,流化床反应器是上下加料,硅烷和氢气从底部注入,硅籽晶从顶部加料,生产的硅颗粒从底部排出,可以做到连续生产,提高生产效率。
其三,流化床法主要从硅烷作为原料,其反应的温度低,分解较为完全,使系统的尾气回收压力大为降低,约700摄氏度以下,而改良西门子法的反应温度高达1050摄氏度,单从这方面看,流化床法就比后者省电不少。
其四,流化床法的的副反应较少,可缩短尾气回收流程,减少投资成本。
其五,流化床法的产品就是颗粒硅,在下一加工环节就可以直接使用,可满足连续投料拉晶工艺的发展。不需要再像改良西门子法那样破碎。
讲了这么多,有人要坐不住了,你说流化床法这么多优点,处处盖过西门子法,为什么历史发展缓慢,且未来难有作为?我们的结论是,你的优势,也许就是你的劣势。
3) “致命”的劣势
不看好改良西门子法的投资者一般的观点就是,能耗大、副产物多,但是这些是可以通过技术改进,逐步改善的。
在能耗方面,多晶硅企业曾被戴上“高能耗”的帽子。今天多晶硅生产全流程综合电耗已经从2009年的200kwh/kg-Si降低至2020年的60kwh/kg-Si,降幅达到70%,有些头部企业甚至已经降到50kwh/kg-Si以下的水平,同时水耗则基本维持在67 kg/kg.Si左右。
同时,值得注意的是,除了老生常谈的电耗和水耗,能耗的综合考虑还需要加上蒸汽消耗。不同于改良西门子法的副产蒸汽用于发电,蒸汽单耗基本上已经下降到0,硅烷流化床法还会使用到蒸汽、天然气等,所以这部分有关蒸汽的25kg/kg.Si左右的能耗仅在生产颗粒硅的时候会产生,需要综合考虑进去,最后,综合能耗算下来,两种技术的能耗差距并不大。
在副产物方面,国内的企业通过技术引进和自主创新,已经可以解决副产物处理问题,实现了物料的循环利用。有头部企业利用甲醇制氢改电制氢、硅粉降耗、余热回收制蒸汽、还原一键启动全过程控制等降耗减排措施,协同多晶硅还原智能控制平台,在高效生产的同时,实现节能降耗,并大幅降低二氧化碳排放量。
但是流化床法的短板还真不是三两下可以彻底解决的,毕竟流化床法也已经诞生了60年。
第一,成品纯度不高。前文讲到,流化床反应器内的硅颗粒是处在悬浮状态,底部不断有气流进入,“沸腾”的硅颗粒会不断冲击反应器内壁,长时间运作下,容易使反应器内部受到腐蚀,常用的金属材料会给反应体系带入大量的金属污染,降低产品纯度。
光是这一点,就让流化床法的企业够忙活一阵了。
一些企业也在研究使用石墨、碳化硅等材质作为反应器内衬或涂覆在金属壁面上,利用其高硬度、不会带入金属杂质等优势,杜绝此环节的金属污染,但这会带来增加投资成本。实际上,在西门子法和流化床法面世后的初期,当时多晶硅市场需求主要为半导体行业用电子级多晶硅,流化床法因为纯度达不到甚至一点机会都没有。
第二,是第一点的延伸,反应器内壁不断受到冲击,容易带来内壁沉积硅粉,造成沾污,甚至造成喷嘴等关键部位堵塞,进而使进气不均匀,不利于反应。在内壁沉积严重的情况下,仍然需要被迫停车进行清理,甚至诱发反应器内壁的破裂。
结果就是目前流化床内件的寿命只有半年到一年,跟还原炉超过20年的寿命比起来简直是快消品。举个不是特别恰当的例子,这就像你去买车,你是选动力一般,但不容易坏的,还是选推背感十足,却动不动要换零件的车。
第三,流化床对安全性的要求很高。硅烷易燃、易爆的突出特点和安全隐患,限制了硅烷流化床法的推广使用。
从发展历程上来看,上世纪70年代,美国联合碳化合物公司,德州仪器公司等又开始对流化床生产工艺进行研究,尤其是美国Ethyl公司(现为Sunedison)于1984年建厂生产电子级颗粒硅,但由于纯度、成本等问题,产能也未能进一步放大。直到21世纪初,随着光伏多晶硅需求的迅速增大,流化床法开始兴起,但是至今未成规模。
流化床法见证了半导体和光伏的光辉岁月,却毫无参与感可言。
一言以蔽之,理论的成本低和工业生产完全是两码事。比如电池最好的一定是氢燃料电池,但工业生产不具备经济性,流化床法的经历过往倒有点类似氢燃料电池,但是至今没有成为主流,氢燃料电池作为锂电池的补充,而氢能作为“终极能源”也是默默的当光伏、风电的备用能源。
虽然流化床法无法成为主流,但是颗粒硅凭借粒径优势,不需要破碎可直接使用,能填补硅块间的空隙提高坩埚装填量,提高拉晶产出,可以作为改良西门子法的补充。
图10:西门子法和流化床法的优劣势比较,资料来源:亚洲硅业科创板上市申请文件的审核问询函回复,广发证券
03 多晶硅企业用脚投票
对于技术路线的选择,全球头部企业的扩产情况已经给了大众一份答案,本文做下总结。
【1】稳定供货的能力
多晶硅的稳定供应是光伏发展的重中之重。
一方面是产品的稳定供货,在供应紧张的情况下,扩产是主旋律。根据国金证券的统计,2022年国内主流硅料企业的90%以上产能均已被下游长单锁定,且最新的硅料长单已经签至2026年,未来几年高比例长单将成为硅料行业的常态。
另一方面,指的是产品质量的稳定性,多晶硅更多的是化工品属性,因此产品的稳定性是最重要的考量,没有之一。这自然涉及到生产的工艺的稳定性、设备的稳定性。改良西门子法工艺成熟稳定,设备也非常成熟,全国投入使用的还原炉达到近千台,远超流化床(全国流化床总数不超过20台)。
【2】长周期视角下,西门子法仍具明显的降成本空间
西门子法未来仍具有明显的降成本空间,我们从几个方向做初步讨论:
1)加大还原炉尺寸
说白了就是进一步提升规模效应。西门子法中,还原炉产量已从1975年的单炉40吨/年,提升至2015年的500吨/年。随着还原炉单炉产能的继续提高和电耗的继续降低,推动改良西门子法继续成为多晶硅行业发展的主导技术。
图11:不同年代的主流还原炉年产量情况,资料来源:公司公告
2)还原炉新型材料的应用
还原炉材料从石英玻璃发展到不锈钢,未来通过使用不锈钢以外的新型材料,或者给内壁镀上反射膜等方式,提高热辐射能的反射率,以提高余热利用率,此方式可实现10%~20%的节电效果,但相应对内壁的材质也提出较高要求,须考虑材质的耐用性及成本问题。
3)闭环生产
由于改良西门子法生成的副产物和尾气较多,影响到生产成本。如何有效循环和处理产物关系到未来的降本方向。比如西门子法生产过程中会产生大量的副产物SiCl4,将SiCl4转化成作为多晶硅生产原料的SiHCl3,从而实现闭环生产,以提高硅粉利用率,降低生产成本。
总之,改良西门子法由于规模化、技术成熟,未来有进一步的下降空间。绝大部分企业仍选择采用改良西门子法进行扩产。正是基于以上认知,CPIA(中国光伏)估算,到2030年,用改良西门子法生产的多晶硅,仍是绝对的主流。本文开篇提出的问题,对应的答案也就跃然纸上了。
图12:国内西门子法(深蓝)和颗粒硅(浅蓝)占比,资料来源:CPIA,华安证券
本文来自微信公众号“锦缎”(ID:jinduan006),作者:知勇,36氪经授权发布。
该文观点仅代表作者本人,36氪平台仅提供信息存储空间服务。
Recommend
About Joyk
Aggregate valuable and interesting links.
Joyk means Joy of geeK