

Baseless Power Modules Clear the Way for a More Electric Aircraft
source link: https://www.allaboutcircuits.com/news/baseless-power-modules-clear-the-way-for-more-electric-aircraft/
Go to the source link to view the article. You can view the picture content, updated content and better typesetting reading experience. If the link is broken, please click the button below to view the snapshot at that time.
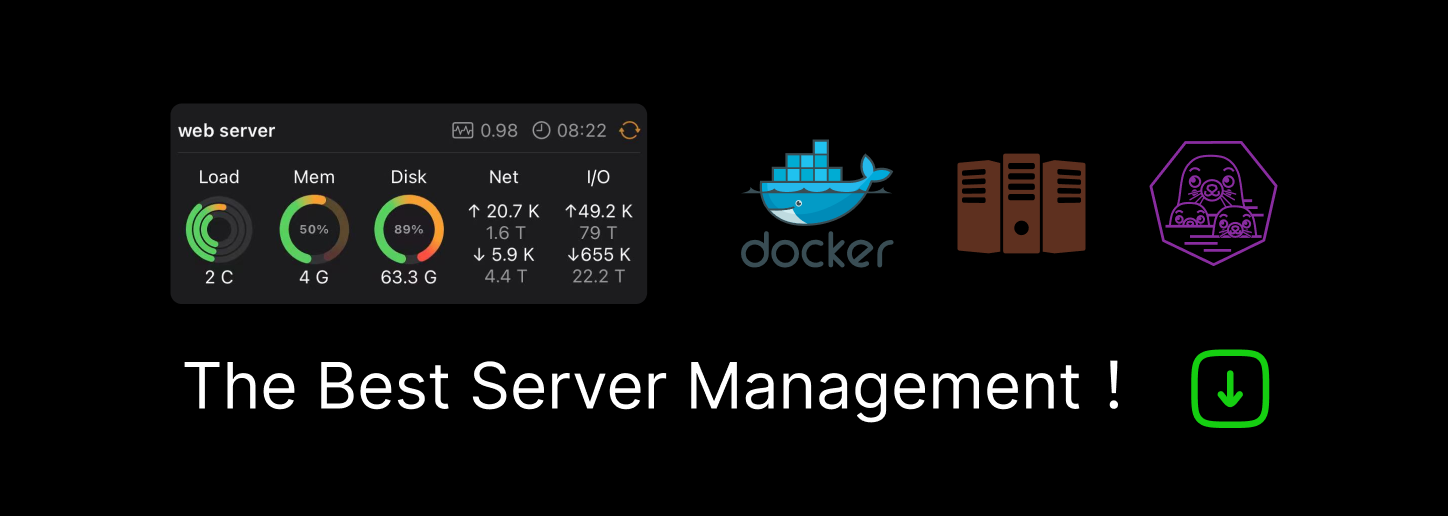
News
Baseless Power Modules Clear the Way for a More Electric Aircraft
The push for greener technology keeps aiming higher, this time targeting avionics. Microchip and Clean Skys have teamed up to create a family of baseless power modules.
Electrification isn't only a hot-button topic in the consumer automotive industry. In response to calls for greener engineering, aircraft manufacturers and suppliers have sought viable methods for reducing emissions.

An example of areas targeted to create more efficient aviation. Image used courtesy of Clean Sky
The relationship between hydraulic power and fuel consumption has thus been increasingly scrutinized. Accordingly, a partnership between Microchip and Clean Sky has birthed a new family of baseless power modules explicitly made for aircraft electrical systems.
These modules aim to usher in next-generation systems based on efficiency and compactness; however, before jumping into this new family, it's essential to understand why the movement towards greener aviation is so important.
The Demand for Greener Aviation
Most of today's commercial airliners are hybridized systems comprised of both mechanical and electrical components.

Examples of electric propulsion systems. Image used courtesy of IATA
The pneumatics and hydraulics found within most planes power several critical in-flight systems, most notably alternators, actuators, and auxiliary power units (APUs).
These parts enable a number of functions, including:
- Flight-control surface adjustments related to elevators, rudders, flaps, landing gear, thrust, and more
- Supplying power to vital electronics and charging the battery, and
- Power generation for avionics, engine starts, and other electrical systems while the plane is idling or encounters an emergency.
The existence of these components is non-negotiable for safe flight and reliable operation. However, that functionality comes with a cost. One Boeing 747 consumes one gallon of fuel per second while in flight; additionally, 57 million flights littered the skies worldwide last year.
Regardless of how fuel expenditures per traveler are calculated, passenger aircraft expel a fair amount of CO2, roughly 915 million tons, in fact, in 2019. That amount accounts for about 12% of all transportation-based CO2 emissions and approximately 2% of all human-caused emissions.
Despite the growing levels of emissions and the global push for change, it is widely recognized throughout the industry that complete engine electrification isn't imminent. Accordingly, some believe that airplane manufacturers won't significantly electrify aircraft engines until 2050, largely due to uncertainties over battery technologies.
Consequently, engineers and companies, like Microchip and Clear Sky, have recognized that component-level design must make adjacent improvements until engines catch up.
Introducing the BL Family of Modules
Incoming electrical systems in planes will require some changes if they're to replace mechanical components. One area of interest is power conversion.
Existing airplanes have two primary electrical circuits and an alternate circuit. These alternating currents feed into a transformer rectifier unit (TRU), which converts them to DC. These AC and DC currents are routed throughout the plane to receiver busses, thus powering the specialized components tied to them.
At this moment, it isn't feasible to replace many moving parts in the power generation system. However, Microchip's BL1, BL2, and BL3 baseless power modules could be a step in the right direction.

Microchip's latest baseless power modules for greener avionics. Image used courtesy of Microchip
Each semiconductor boosts AC/DC (and vice versa) conversion efficiency and power generation; their silicon carbide construction is also 40% lighter than market alternatives. All three devices meet Radio Technical Commission for Aeronautics (RTCA) guidelines, and Microchip claims that they're 10% cheaper than metal-baseplate modules.
In addition to those features, they're also low profile, which is critical within a complex, densely packed electrical system.
Designers can easily solder them onto printed circuit boards, especially since soldiered connections are less susceptible to cracking and deformation during high-wattage temperature cycling. They're also more performant when operating at higher temperatures, thanks to improved heatsinking.
Since all three modules are the same height, it's easier for them to be paralleled into a three-phase bridge, as well as other topologies, to create higher-performing power inverters and converters.
A final key feature is their low inductance, or rather, the chip's tendency not to oppose changes in electrical currents passing through its circuitry. The BL family's lowered inductance thus equates to higher power density.
Despite the overall features already covered thus far, the next section will briefly outline even more key specifications.
Quick Specifications
The BL module family is MOSFET by design, and changing voltages determine how each semiconductor conducts electricity.

An example overview of the MSCSM120AM31CTBL1NG, a baseless SiC MOSFET module included in the BL1 family. Image used courtesy of Microchip [Datasheet PDF]
It's the most common transistor in digital circuits today, and the technology excels at either switching or amplifying incoming signals.
Additionally, Schottky barrier diodes are incorporated to increase efficiency in the 100 W to 10 kW range.
They’re available in the following configurations:
- Phase leg
- Full bridge
- Asymmetric bridge
- Boost
- Dual common source
MOSFETs and IGBTs in the family operate at ranges from 600V to 1200V, while accompanying rectifier diodes operate at up to 1600V. They're tailor-made to complement other Microchip aerospace technologies, like drive controllers, storage ICs, FPGAs, microcontrollers, microprocessors, and more.
While this family hopes to open the door for future cleaner technology, there is still a lot more electronics and design that needs to be done.
Pursuing a Cleaner Future
Without a doubt, Microchip's efforts have stemmed from increased demands for aircraft modernization. There's a significant push to electrify aircraft and decrease their collective environmental footprint, especially as air travel grows cheaper and more popular, with annual flights increasing worldwide for over a decade now.
There's an acknowledgment that change will be gradual for the time being. However, companies like Microchip (and especially EU bodies) have committed to developing transitional technologies for the decades to come. It will be interesting to see what technology comes out on both the component level and in the case of large-scale system design.
Recommend
About Joyk
Aggregate valuable and interesting links.
Joyk means Joy of geeK